Cobots – Mensch und Roboter gemeinsam zum Erfolg
EMO Hannover 2019 zeigt Robotik- und Automationslösungen für Fertigungsbetriebe
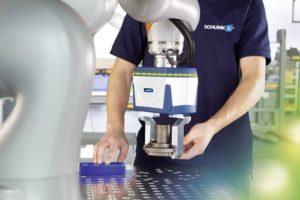
Frankfurt am Main, 12. Juni 2019. – Um als Unternehmen international erfolgreich zu bleiben, gehören Robotik und Automation zu den Schlüsseltechnologien. Cobots interagieren dabei direkt mit dem Menschen und unterstützen Fertigungsbetriebe, sich im Markt produktiv zu behaupten. Auf der EMO Hannover 2019 finden Fachbesucher zahllose Automatisierungslösungen und kollaborative Roboter zur Steigerung ihrer Produktivität.
Mithilfe von Automation und Digitalisierung lassen sich Fertigungsprozesse effizienter gestalten. Von besonderem Interesse sind in diesem Umfeld Cobots – die kollaborativen Industrieroboter arbeiten gemeinsam mit den Menschen ohne spezielle Schutzeinrichtungen wie Zäune oder abgegrenzte Bereiche. In welchen Prozessen kommen Cobots bereits zum Einsatz? Wie lassen sich Kollisionen und damit mögliche Verletzungsgefahren vermeiden? Robotikhersteller, Anbieter verschiedenster Peripheriekomponenten für Automationslösungen sowie Sicherheits- und wissenschaftliche Experten geben einen aktuellen Einblick und Prognosen für künftige Entwicklungen.
Mitarbeiter ergonomisch entlasten
„Für eine intelligente Produktion ist der Mensch unerlässlich“, so Jochen Vetter, Manager Robot Safety bei der Pilz GmbH & Co. KG aus Ostfildern. „Roboter übernehmen z.B. körperlich anstrengende oder monotone Tätigkeiten, während der Mensch höherwertige Aufgaben ausführt. Damit kann die Automatisierung auch Antworten auf Fragen geben, die der demografische Wandel aufwirft.“ Für die Validierung sind bei der Mensch-Roboter-Kollaboration (MRK) unterschiedliche Methoden anzuwenden. Beispielsweise muss zwingend durch ein Messverfahren ermittelt werden, ob mögliche Kollisionen sicherheitstechnisch unbedenklich sind. Hierfür hat Pilz eine eigene Methodik erarbeitet. Ein System misst u.a. die auf den menschlichen Körper einwirkenden Kräfte und vergleicht sie mit den Grenzwerten gemäß der Norm für kollaborative Roboter ISO/TS 15066.
„Die Herausforderung besteht darin, dass sich die Grenzen zwischen den Arbeitsbereichen von Mensch und Maschine auflösen. Zusätzlich zu den vom Roboter ausgehenden Gefahren müssen die Bewegungen des Menschen Berücksichtigung finden“, weiß der Robotik-Sicherheitsexperte. „Diese sind nicht immer kalkulierbar in Hinsicht auf Geschwindigkeit, Reflexe oder plötzlichen Zutritt zusätzlicher Personen. Kollisionen dürfen jedoch zu keinen Verletzungen führen.“ Voraussetzungen dafür seien zuverlässigere Steuerungen und intelligente, dynamische Sensoren am Roboter. Zudem gelte es, durch normative Grundlagen verlässliche Sicherheitsstandards zu setzen.
„Die Interaktion wird sich in Richtung ‚natürlich‘ entwickeln, etwa bei der Sprache und Gestik“, ist Vetter überzeugt. „So wird die MRK für ein anderes Agieren auf eine neue Qualitätsebene gebracht. Darüber hinaus werden MRK-Lösungen in Zukunft an die Fabriksteuerung via OPC UA oder die Industrie 4.0-RAMI-Standards angebunden sein. Sinnvolle Einsatzgebiete sind eher nicht in der Großserienproduktion, sondern bei mittleren und kleinen Serien angesiedelt. MRK macht dann Sinn, wenn die Mitarbeiter ergonomisch entlastet werden, etwa bei Wartungsarbeiten.“
Werkstücke bis 8 kg greifen dank Sicherheitsintelligenz
„Aufgrund der biomechanischen Limits – vorgegeben durch die ISO/TS 15066 – konzentrierte sich der Einsatz von Cobots bislang auf das Handling von Kleinteilen, etwa in Montageanwendungen der Elektronikindustrie oder beim Pick & Place von Gehäusen, Dreh- und Frästeilen etc.“, weiß Prof. Markus Glück, Geschäftsführer Forschung & Entwicklung, Chief Innovation Officer bei der Schunk GmbH & Co. KG, Lauffen/Neckar. „Mit unserem Großhubgreifer EGL-C erschließen wir nun aber eine neue Bauteildimension: Erstmals ist es möglich, formschlüssig gegriffene Werkstücke bis 8 kg sicher zu handhaben. Damit ergeben sich große Potenziale, auch bei Werkzeugmaschinen oder in der Montage.“ Dank integrierter und zum Patent angemeldeter Sicherheitsintelligenz ist es beim Co-act (collaborative actuator) EGL-C gelungen, in kollaborativen Anwendungen Greifkräfte bis 450 N zu realisieren. Das ist rund dreimal so viel wie bisher und stellt eine Weltneuheit dar – auch zu sehen auf der EMO Hannover 2019. „Die MRK wird die Arbeitswelt radikal verändern“, prognostiziert Prof. Glück. „Im Mittelpunkt stehen die Verbesserung der Ergonomie, flexiblere Arbeitsprozesse, Effizienzsteigerung sowie Prozessoptimierung. Mithilfe intelligenter Greifsysteme lassen sich künftig auch höhere Bauteilgewichte handhaben. Zudem werden dank 24V-Technologie Einsätze auf mobilen Plattformen an Bedeutung gewinnen. Ein großes Wachstumspotenzial besitzt darüber hinaus die Montageassistenz durch Leichtbauroboter.“
Eine neue Ära bei der Beladung von Werkzeugmaschinen
„Kollaborative und mobile Robotersysteme bieten neue Möglichkeiten für die Automation von Werkzeugmaschinen. Erstmals kann sich die Automation von ihrem starren Korsett lösen und dank innovativer Robotiklösungen eine Flexibilität und Produktivität in nie gekannter Dimension erreichen“, berichtet Peter Pühringer, Division Manager bei Stäubli Robotics in Bayreuth. Um diese Flexibilität auf die Spitze zu treiben, hat Stäubli die neue TX2-Sechsachser-Generation so universell wie möglich ausgeführt. In der neuen Ausführung eignen sich diese Roboter für die direkte Zusammenarbeit mit dem Menschen. Zudem sind sie als mobile und gleichzeitig kollaborative Robotersysteme erhältlich. „Damit läuten wir eine neue Ära in der Beschickung von Werkzeugmaschinen ein“, ist Pühringer überzeugt. Die Roboter arbeiten sowohl im Stand-alone-Betrieb als auch direkt mit Maschinenbedienern zusammen. Sie können in mobiler Ausführung auf einfachste Art unterschiedliche Werkzeugmaschinen verketten und den kompletten Workflow in Industrie 4.0-Umgebungen übernehmen. „Mit dieser unglaublichen Flexibilität lassen sich völlig neue, digital vernetzte Produktionsprozesse darstellen“, so Pühringer. „Diese werden zu einer signifikanten Steigerung der Produktivität führen und die Wettbewerbsfähigkeit innovativer Unternehmen auf eine neue Stufe stellen. Auf der EMO Hannover stellen wir diese Lösungen einem breiten Publikum vor.“
Sensoren vermeiden mögliche Kollisionen
„Cobots kommen derzeit häufig für einfache Handhabungsprozesse zum Einsatz, u.a. für die Beladung von Maschinen. Dabei werden sie zwar oft schutzzaunlos, aber dennoch mit zusätzlichen Sicherheitseinrichtungen ausgestattet und weniger in einer direkten Mensch-Roboter-Kooperation eingesetzt“, weiß Prof. Gunther Reinhart, Inhaber des Lehrstuhls für Betriebswissenschaften und Montagetechnik am iwb (Institut für Werkzeugmaschinen und Betriebswissenschaften) der TU München. „Aktuelle Arbeiten beschäftigen sich mit der Planungsunterstützung für die MRK, der Sicherheit, aber auch der Instruktion der Roboter. Bezüglich der Sicherheit gehen Innovationen dahingehend, dass mögliche Kollisionen vor Berührung durch unterschiedliche Sensoren – wie kapazitive oder Ultraschallsensoren – oder aber kamerabasiert detektiert werden.“ Der Umgang mit den aktuellen Normen sei derzeit vielen Firmen unklar. „Dabei ist insbesondere zu nennen, wie die Werte in der ISO/TS15066 behandelt werden sollen“, so Reinhart. „Sind die rechtlichen Fragestellungen der Arbeitssicherheit geklärt, werden kollaborative Roboter wohl überwiegend in der Montage zum Einsatz kommen“, wagt Reinhart einen Blick in die Zukunft. „Weitere Anwendungsfälle beziehen sich insbesondere auf eine ergonomische Unterstützung. Dazu muss es jedoch zunächst mehr Roboter für eine MRK mit höherer Traglast geben. Das Institut für Werkzeugmaschinen und Betriebswissenschaften steht den Fachbesuchern der EMO Hannover 2019 für nähere Erläuterungen sehr gerne zur Verfügung.“
Autor: Dag Heidecker, daxTR – Technik + Redaktion, Wermelskirchen (nahe Köln)
((Umfang: rund 7.700 Zeichen inkl. Leerzeichen))