Data themed around the tool ensure transparent production
High-precision tools have a key function in digital production operations. Application-tailored integration into the production sequences and purposeful processing of the tool data are the basis for up-to-the-future Industry 4.0 solutions.
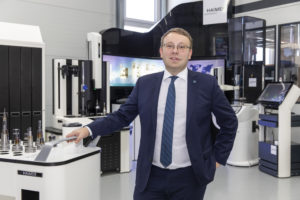
METAV 2020 to showcase the practical utility of digitalisation and automation in tool provision.
The digitalisation of production processes plays an important role for every company that wants to operate successfully on the market. Since the tool with its specific data is in metal-cutting machining a crucial constituent of the process chain, it has to fit in with the digital production environment. “All digital options have to be rigorously implemented – from the tool itself, then the tool-holder, including the clamping operation and balancing, all the way through to tool presetting and deployment on the machine,” is how Andreas Haimer, General Manager of Haimer GmbH, Igenhausen, summarises the spectrum involved.
One important approach in this context is the provision of digital services by tool manufacturers for their customers, e.g. by ensuring that all tool data can be retrieved online. According to Andreas Haimer, moreover, a tool management solution that enables a digital workflow of the tool data is crucial. This means: the software has to be able to integrate the entire tool environment – shrink-fitting, balancing, presetting – into the digital process and render it automatable.
Exchanging tool data beyond the boundaries of individual facilities
One thing is certain: digitalisation is transforming the entire production sequence. With the aid of tool data stored in memory, the entire manufacturing process can be simulated and optimised in advance. Storage systems are often connected, too, and the location of each individual tool can be tracked. “The bottom line is that thanks to digitalisation in their production operations companies save time, money and resources,” says Bernd Schwennig, Technical Sales Manager at E. Zoller GmbH & Co. KG, Pleidelsheim, a member of the GTDE association (Graphical Tool Data Exchange – Standard Open Base), which has taken on board the issue of data exchange under the aegis of the VDMA’s Precision Tools Association.
The foundation for every automation process is always the tool data, which meanwhile subsume much more than merely the geometrical data. Besides machine-specific data, these include, for example, the remaining service lifetime available, or the storage location or magazine space on the machine. “These data are, of course, available worldwide, if the company so desires,” adds Bernd Schwennig. It must, moreover, be assumed that the data inside a company are increasingly being exchanged beyond the boundaries of individual facilities. “That a purchase order is triggered at a tool vendor when stock levels in a production plant fall below a minimum inventory is, of course, only a minor aspect here, but one that’s already in actual use. Overall, the entire interchange procedures are much more open. Needless to say, this in its turn entails quite different challenges,” he adds in conclusion.
Logistics for tool supply to the machine are being optimised
“In digital production operations, too, the metal-cutting process as such is still crucially influenced by the tool in terms of component quality and cost-efficiency. The tool thus remains a crucial factor for success in metal-cutting production operations,” adds Dr. Steffen Lang, who heads the Service Division at Gühring KG in Albstadt.
The digital integration of metal-cutting machines enables the performative capabilities and the current status of the tool deployed in the machine to be acquired far more precisely than hitherto. Thanks to the resultant transparency, the entire logistics for tool supply to the machine can be optimised. Dr. Lang summarises the extent of an automated tool provision feature: “This begins with presetting of the tools actually required at the machines, which are mounted and adjusted in the optimal sequence. It continues with consumption monitoring of the inventory levels and acquisition of service lifetime changes and factoring them directly into further tool planning. And finally the consumption and performance data are forwarded to the vendors, so as to optimise the tool’s performance and supply.”
In this context, Gühring offers a machine interfacing concept that enables the machine status and technological process parameters like spindle speed and torque, plus forces of the feed axes, to be acquired. Moreover, the machine data can be acquired directly in the production process, and on this basis the metal-cutting process can be immediately optimised.
Solutions for digitalisation in the tool environment
In order to progress digitalisation, moreover, the company has developed for its products a tool management software package of its own that executes and organises the exchange of setpoint and actual values, and other tool data, between the individual stations in the tool room and the company’s network. Haimer’s devices from the Industry 4.0 series, moreover, can be automated using modern digital features and interfaces.
For Zoller, the paramount focus is on holistic tool data handling. The company’s setting and measuring devices determine the requisite tool geometry data, and edit them so that the machine tool can read them in. “Even for this step of data transfer, we offer a wide range of highly disparate solutions for every size of firm. The data can be both entered manually and transmitted over a network or an RFID chip,” reports Bernd Schwennig. The tool management capability subsumes not only the organisation of tool storage, but also evaluation options, e.g. for service lifetime or costs of tool utilisation, broken down into a specific order or even a specific component. “Our goal is always to generate maximised transparency in the entire tool context, so as to optimise the production sequences involved and render them faster and more cost-efficient,” says Bernd Schwennig.
Users have to familiarise themselves with and harness the functionalities involved
But users, too, have to engage with the issue of digitalisation. For new investments, in particular, companies should take care to ensure that every element in the tool’s environment has Industry 4.0 capability and can be integrated into the digital workflow. “A tool should, for example, be unambiguously identifiable using RFID data chips or using QR or data matrix codes, and through this detection capability supply further tool data like Article Number or 3D models,” says Andreas Haimer, citing specific key data. Bernd Schwenning adds: “The most important factor for optimal tool deployment is properly updated tool data. Without tool data, the entire sequence is inconceivable: neither digitally aided inventory management nor the retrieval of metrological programs nor reading tool data into the machine.” This first step, of course, he admits, is tediously hard work, but it does offer the requisite foundations for corporate survival in the future.
Online monitoring of the machine parameters determinant for the metal-cutting process, like torque and power consumption of the spindle, feed forces of the axes, etc. enables tool utilisation to be optimised or the dimensioning of the tool to be rendered more suitable for the machining job involved. “Both provide the user with an option for raising his productivity more selectively. It’s important for him to know and exploit these advantages of machine interfacing, so as to upgrade his competitiveness,” emphasises Dr. Steffen Lang.
Exhibitors to showcase up-to-the-future digitalised solutions
At the METAV, the exhibitors will in the context of tool utilisation also be presenting disparate solutions in digital production operations. For instance, Haimer will be showcasing its concepts in regard to the digitalisation of tool presetting, networking and concatenation of systems. Moreover, the company will be presenting many new tools and holders, and in its role as a complete-system vendor for everything to do with machine tools be spotlighting at the fair the very latest shrink-fit, balancing and presetting devices.
Zoller will be showcasing solutions for measuring and managing tools, and for tool data management. This involves metrology, software and services that guarantee complete-system solutions for adjusting, measuring, testing and managing metal-cutting tools. In addition, the company provides information on automation solutions that support daily tool handling for enhanced process reliability.
On the Gühring company’s stand, the machine’s interfacing with the tool management software and the evaluation of machine data acquired will be on show live on the spot on a CNC machine. Further exhibits from the Gühring company will be new drills and metal-cutting concepts for the field of e-mobility.
Size: around 9,000 characters incl. blanks
Author: Annedore Bose-Munde, Specialist Journalist from Erfurt, on behalf of the VDMA Precision Tools Association
Categories: 2020