EMO Hannover TRENDSPOTS – Discover the product innovations of the world of metalworking: No. 2
Batch size one – and quick about it!
In the run-up to EMO Hannover 2019, BAM GmbH is launching its new digital manufacturing platform up2parts. This online portal for custom manufacturing components aims to eliminate time-consuming e-mail inquiries and lengthy purchasing timeframes.
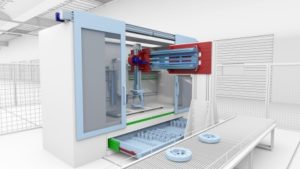
BAM GmbH specializes in using mechanical machining and additive manufacturing processes to produce complex metal and plastic components to the tightest of tolerances. As digitization and Industry 4.0 have gathered pace, the company’s portfolio has also grown and now covers everything from individual prototypes to high-volume production. Skilled specialists use high-tech machines to turn and mill a range of items, including highly specialized components for laboratory equipment, sensors and connection technologies. An in-house research and development department also works continuously on innovative solutions for the traditional manufacturing and mechanical engineering industries. The up2parts.com online portal marks a further milestone in the digital revolution for the manufacturing sector in the run-up to EMO Hannover 2019.
The new up2parts portal is an easy-to-use tool for ordering custom-made components, thus heralding an end to time-consuming e-mail inquiries and lengthy purchasing timeframes. It is designed to ensure no one will have to wait extra hours or even days to get costings or quotes. Companies and private individuals alike can upload their 3D data model and find out in less than a minute how much the component will cost. “No matter whether components are produced using mechanical machining processes or additive manufacturing, our machine learning algorithms calculate each price quickly and reliably,” says Marco Bauer, Managing Director of BAM GmbH.
This development is the result of a fully integrated approach to the purchasing and manufacturing process. According to the company, even complex components can be created online with just a few mouse clicks. “At the heart of the costing process is our complexity factor, which is evaluated using artificial intelligence and is based on data from our company’s eight years of technical manufacturing expertise,” says Dr. Christian Heining, Head of Research & Development. What’s more, up2parts guarantees lasting data security, with all servers located in European data centers and meeting international and country-specific standards.
BAM GmbH (92637 Weiden, Germany), Hall 9, Stand F32
Contact: Marco Bauer
Tel.: +49 961 6000-0
Smarter lubrication
Castrol is unveiling SmartControl – a new, extensively automated solution for intelligently managing metalworking fluids.
When working in any technical field, you’re bound to come across a whole host of confusing abbreviations, some of which will even leave insiders a bit baffled. And yet many of these can relate to important factors that directly influence productivity and efficiency, such as MWF, which stands for “metalworking fluids”. It certainly can’t hurt to take a closer look at what lies behind the abbreviation – which is exactly what Castrol has done. “We at Castrol know that managing cooling lubricants involves numerous manual processes. These include sampling, testing, control measures and documentation, for instance, which isn’t an efficient use of our customers’ time and resources. That’s why we’ve developed Castrol SmartControl – our automated solution for real-time condition monitoring. When using Castrol SmartControl, our customers can manage their cooling lubricants much more effectively and efficiently and limit the associated HSSE risks,” explains Mathias Buschbeck, Global Industrial Strategy Implementation Leader at Castrol.
SmartControl is thus a smarter way to manage the condition of water-miscible metalworking fluids. For example, it frees employees up from having to carry out repetitive, time-consuming and hazardous tasks. It works by integrating XBB cooling lubricant technology from Castrol with advanced Industry 4.0 technology in the form of real-time condition monitoring. This makes it possible to optimize MWF management and minimize faults. SmartControl continuously measures the concentrations, pH values, conductivity, temperatures and volumetric flow rates of metalworking fluids. Any deviation from the specification sends an immediate warning to company and production IT systems. As SmartControl does not require manual sampling, no time is lost getting samples to a lab and therefore there are no delays due to late report shipping. What’s more, it cleans and calibrates itself, thus ensuring continuous precision.
Castrol Lubricants UK Ltd. (Mitcheldean, Gloucestershire GL17 OUQ, UK),
Hall 6, Stand H51
Contact: Andreas Osbar
Tel.: +49 40 6395-2222
Mighty fine!
BIG KAISER, a supplier of high-precision tooling systems, is at EMO Hannover 2019 to showcase its innovative portfolio of precision tools and tool holders, including the new EWA – an intelligent, fully automatic fine boring tool.
BIG KAISER Präzisionswerkzeuge AG from Switzerland, a world-leading supplier of high-precision tooling systems and solutions for the metal-processing industry, is exhibiting its range of innovative precision tools and tool holders at EMO Hannover 2019. The highlight of the company’s presentation at the show is the live demonstration of its new intelligent, fully automatic EWA fine boring tool on a FANUC CNC machine. The EWA benefits from fully automatic operation, with no need for a human operator, and does not have to be stopped to perform measurements or manual fine boring tool adjustments. This results in extremely fast, accurate and cost-effective fine boring that saves users a great deal of time. Another automatic model on show is the EWE Downsize, the world’s smallest digital fine boring head, which connects wirelessly to smartphones, tablets and even smart watches via an app.
That’s not all, though. Visitors to BIG KAISER’s stand can also see the highly accurate HSK-E50-HDC hydraulic chucks and the updated version of the HDC-J Hydraulic Chuck with Switchable Coolant Supply for high-precision cutting. In addition to peripheral cooling, Jet-Through Hydraulic Chucks now also deliver coolant centrally. Another exhibit is the company’s new MEGA Micro Coolant Nut for the MEGA Micro Chuck 6S, which supplies coolant more efficiently to the micro cutting tool and has ideal credentials for high-speed micro machining down to diameters of just 6 millimeters. BIG KAISER’s CEO Reto Adam underlines his company’s leading role in developing precision tools and tool holders with highly advanced mechanical and electronic control technologies and is looking forward to welcoming visitors from all over the world to the trade show. “We invite our friends, colleagues and customers to come to EMO Hannover and see how we are applying our unique expertise to our latest products,” he says.
BIG KAISER Präzisionswerkzeuge AG (8153 Rümlang, Switzerland),
Hall 3, Stand B14
Contact: Marco Martinaglia
Tel.: + 41 448179270
An elite partner with something for everyone!
At EMO Hannover 2019, BURKHARDT+WEBER is exhibiting a powerful horizontal MCX machining center with integrated pick-up station to demonstrate its transformation from a machine manufacturer pure and simple to a technology partner for its customers.
By its own admission, BURKHARDT+WEBER (BW) has spent the past two years focusing on establishing an unusually small series of machines by its own standards, but it is now once again pulling out all the stops at EMO Hannover 2019. Among other things, the company is using the world’s premier trade fair for the metalworking sector to show what it believes BW is now all about, with strong, highly individualized machining centers adapted to customer requirements – entirely in keeping with the “Customized by BW” brand claim.
The concept of BW’s highlight at this year’s trade show is therefore responding to its customers’ calls for a machine that can handle particularly long and heavy tools with large diameters while also complying with the stringent dimensional and positional tolerances of the electric motor housing. Since it was also necessary to support boring depths of up to 1,100 millimeters in conjunction with diameters of 680 millimeters – dimensions that quickly add up to a tool weight of over 75 kilograms – much originally pointed to a vertical turning machine being the best fit. The innovative solution ultimately devised in collaboration with EMOD Motoren GmbH was admittedly very different, combining a powerful horizontal MCX machining center and a pick-up station. At the end of the day, this pairing promises greater flexibility and higher productivity. Visitors to EMO Hannover 2019 who now also see themselves more as technology partners than machine manufacturers pure and simple can see this sophisticated system in all its glory. “Nowadays, people want more than iron and steel – especially in the case of large machining centers that often represent a significant and strategic investment for customers. Our projects aren’t simply about the machine, but more about a holistic, forward-looking concept that requires us to become something akin to a system supplier. This involves considerations such as process optimization, integrated production and – naturally – digitalization,” says BURKHARDT+WEBER’s Sales Manager Michael Wiedmaier in reference to the company’s latest development.
BURKHARDT+WEBER Fertigungssysteme GmbH (72760 Reutlingen, Germany), Hall 12, Stand D36
Contact: Alina Bachofer
Tel.: +49 7121 315-0
Roll on over!
In addition to automatic machine doors and efficient motion concepts for workpiece handling systems – ROLLON GmbH is at EMO Hannover 2019 to showcase its “Seventh Axis”, designed to provide increased freedom of movement to future handling robots.
Industrial linear systems must be able to operate reliably over a long period of time – often with high working cycles and under critical conditions. To keep maintenance work and costs to a minimum, they should also be easy to assemble and replace if necessary. Based in Düsseldorf, ROLLON GmbH promises to deliver solutions that fully meet these requirements. Some forty years after it was founded, this globally operating company is now one of the leading end-to-end suppliers of linear technology solutions, offering one of the most comprehensive ranges of linear guides, telescopic rails and linear axes. It is now attending EMO Hannover 2019 to showcase its portfolio of modular linear solutions for automating industrial machinery. In addition to automatic machine doors and efficient motion concepts for workpiece handling systems – the ROLLON “Seventh Axis” for handling robots is taking center stage at the fair.
With this concept, ROLLON aims to considerably expand the operating range of industrial robots in the future. The solution has the entire robot move along a linear axis, which expands its operating range so it can perform tasks in several different places. Available in seven sizes, the shuttle system features a modular design and supports long distances and high dynamics. According to its makers, it can be easily integrated into existing scenarios and move any type of robot weighing up to 2,000 kg.
ROLLON GmbH (40589 Düsseldorf, Germany), Hall 8, Stand D20
Contact: Susan Gabriel
Tel.: +49 4181 92892-0
The future is smart!
SICK is gearing up for the smart production structures of the future – developing intelligent sensors that gather data and evaluate it in real time, adapt to their environments, communicate in networks and perform automation functions independently.
SICK AG is one of the world’s leading manufacturers of sensors and sensor solutions for industrial applications. At EMO Hannover 2019, it is unveiling intelligent sensors that pave the way for smart tasks by independently performing automation functions. Further innovative highlights include high-performance integration solutions with serious computing power and impressive connectivity for future-proof implementation of Industry 4.0. What’s more, a new software product makes it possible to configure and monitor smart sensors in machine tools to provide effective support for edge computing concepts.
As data sources for the smart factory, the smart sensors and system solutions on show in Hannover are intended to demonstrate how digitization solutions can be put into practice in machine tools. To ensure sensors and machines can communicate with each other at all and to make processes transparent, SICK offers a whole range of scalable integration solutions. The Telematic Data Collector TDC-E, for example, is a gateway system for multisensor networking equipped with mobile communications options boasting enhanced functions for capturing, processing and transmitting process and sensor data. The data collected, analyzed and individually visualized by the TDC-E should make the operational status of the networked sensors situated in a machine tool, together with the processes in which they are used, entirely transparent. Meanwhile, the Sensor Integration Machine from the SIM1012 product family aims to open up new possibilities for applications in smart machine tools, both today and in the future, thanks to its IoT gateway functionality and adaptive multisensor integration. These two integration solutions make it possible to transfer process-, production- and business-related data directly to Ethernet fieldbuses or the cloud.
The Integration Solutions FieldEcho software tool, which is also being showcased at the trade fair, features a web-based graphical user interface (GUI) designed for parameterizing and monitoring all IO-Link devices in a machine tool or plant. The enhanced accessibility and transparency of the IO-Link data boost flexibility and availability, while the easy connection via the PLC’s OPC-UA server promises to transform FieldEcho into a future-proof integration solution.
Sick AG (79183 Waldkirch, Germany), Hall 9, Stand F32
Contact: Melanie Jendro
Tel.: +49 7681 202-4183
Kessler has no time for bigheads!
Kessler, a system supplier for the machine tool industry, is at EMO Hannover 2019 to showcase its new MINI compact head. This latest addition to the company’s Head line was designed to make the most of a machine’s working space.
Kessler is well known in the sector for supporting its customers with modular products for specific requirements. In addition to high-speed rotary and rotary tilt tables, the company’s portfolio also includes directly driven 2-axis heads complete with integrated high-tech spindles. In-house production ensures all modular components are equipped with the latest generation of Kessler motors. To coincide with EMO Hannover, Kessler is systematically adding to its modular range of 2-axis heads, motor spindles and rotary tilt tables. The 2-axis heads from the company’s Head line are a real highlight.
A highly dynamic powerhouse achieving speeds of up to 20,000 rpm, the new MINI compact 2AH being unveiled in Hannover has the ability to reach locations that are difficult to access when machining workpieces with complex geometries or contours. This compact entry-level 2-axis head is equipped with spindles that were deliberately designed to be very short so as to increase the working space in the machine.
Kessler recommends the short MT line spindle for machining workpieces large and small made of various materials. This spindle was developed specifically for use in directly driven, tilting 2-axis heads to generate a high power density in the smallest of spaces. The low interference contour is designed to enable the MT line to machine larger workpieces in the same working space. The spindle – which is optionally available with shaft clamping for high-precision turning operations – is also intended for machining with long boring bars.
KESSLER Group (88422 Bad Buchau, Germany), Hall 9, Stand E70
Contact: Börne Rensing
Tel.: +49 7582 809-0
Big news for big machining jobs!
A real highlight among the extremely efficient die- and mold-making solutions Okuma is exhibiting at EMO Hannover 2019 is the new MCR-S (Super) double-column milling center for the high-precision 5-sided machining of large workpieces.
As the only end-to-end supplier in its sector, Japan’s Okuma Corporation is showcasing a whole host of other CNC machine tools, software solutions and intelligent control systems along with its new MCR-S (Super) double-column milling center at EMO Hannover. This milling center has been singled out because it combines several high-end functions and is designed to be perfect for machining press dies to the highest standards.
The developers’ aim is for future users of the MCR-S to benefit from exceptional dimensional accuracy and excellent surface quality. The sturdy double-column design also optimizes stability and vibration damping. The process of manufacturing press dies is susceptible to temperature fluctuations, so the MCR-S has a thermo-friendly concept to compensate for thermal deformations. It also boasts a swivel image sensor that is designed to ensure highly accurate measurements at the cutting edge position and easy traceability of all steps. What’s more, according to Okuma, hyper-surface technology helps eliminate manual finishing, which means the raw material can be processed faster – not least thanks to the high cutting capacity of the MCR-S, which is designed to achieve an impressive face milling speed of 710 cm/min.
Okuma Corporation (JPN-Aichi-Pref. 480-0193, Japan), Hall 27, Stand D26
Contact: Norbert Teeuwen
Tel.: +49 2151 374-0
A new era in print-ready strength
Swedish-based VBN Components AB sees the Additive Manufacturing Circle at EMO Hannover 2019 as the perfect place to launch its new alloy Vibenite 480, said to be unique in the world of additive manufacturing.
VBN has declared itself the only company in the world that can print fully functional components in carbide using EBM technology – and it is coming to Hannover. By showcasing its Vibenite 480 alloy, the Swedish company aims to prove it is already possible to 3D print materials with an extremely high carbide content. The new metal is said to contain 65 percent carbides, which the company claims is unrivaled in additive manufacturing and even considered “impossible” by some. The carbides are small and well dispersed so that a tougher structure can be achieved compared to conventional sintered carbides. According to the company, the corrosion-resistant material has a hardness of ~ 66 HRC that has been measured with a long-term heat resistance of 750 degrees Celsius.
The engineering innovation is claimed to enable rapid product development for components such as gear hobs and rock drills. What’s more, since the manufacturing process is not restricted by chip-forming machining processes, pressing operations or sintering, product developers can let their imaginations run wild. Besides all that, the efficiency of 3D printing makes it far more environmentally friendly than conventional methods. Vibenite 480 is based on a metal powder that is produced on a large scale using gas atomization, which reportedly minimizes both costs and environmental impact. The new material, which combines the toughness of powder-metallurgical high-speed steels (PM-HSS) with the heat resistance of carbides, is also known as a hybrid carbide. “It is a particular kind of satisfaction to be able to offer our new hybrid cemented carbide to customers who have been asking for this for some time now,” says Ulrik Beste, CTO and one of VBN’s founders, before adding: “We are starting a new era in Swedish material history!”
VBN Components AB (75228 Uppsala, Sweden), Hall 9, Stand H20
Contact: Isabelle Bodén
Tel.: +46 702 362281
Made for you!
Spanish company Soraluce S.Coop. is showcasing a complete philosophy at EMO Hannover 2019 under the banner #MadeForYou. It aims to unlock added value for its customers day in, day out.
Visitors to the Soraluce S.Coop. stand at EMO Hannover can see for themselves the four core areas that make up the company’s customer-centric approach #MadeForYOU. Alongside “Intelligent Machineplus” with its groundbreaking machining solutions and “Multitask / Multitalent – All in one”, where it’s all about milling, turning and grinding with a machine, there is valuable information about practice-based services on offer under the banner “Service with a passion”. Finally, the “Precision” area shows how every customer can create their own masterpiece.
Soraluce S.Coop. is also looking to use EMO Hannover 2019 to show the world that it is constantly rising to the challenge and is committed to continuing to set key milestones in the machine tool industry with its unique and intelligent technologies. Once again, Soraluce is keen to impress visitors in Hannover with a lively showcase of high-quality products and customer-oriented services. The customer is at the heart of everything. With its #MadeForYOU initiative, the company aims to meet specific customer needs to unlock added value for its customers day in, day out.
Soraluce S.Coop. (20570 Bergara (Gipuzkoa), Spain), Hall 13, Stand B38
Contact: Maite Riaño
Tel.: +34 943 76 90 76
Mobile: +34 688 88 75 96
For photos and video clips, visit: Trendspots – Product Innovations
Categories: Allgemein