Mysterium um Kegelräder teilweise gelüftet
Julia Mazak wird auf EMO Hannover 2019 für Projekt des Jahres ausgezeichnet.
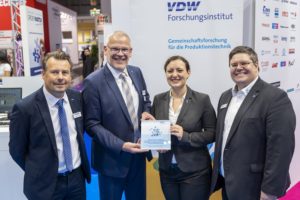
Gestern nahm Julia Mazak vom Werkzeugmaschinenlabor WZL der RWTH Aachen die Auszeichnung des VDW-Forschungsinstituts für das „Projekt des Jahres“ entgegen. Mazak hat erstmals systematisch untersucht, wie die Werkzeugeinsatzdauer für Kegelräder, die der Übertragung von Leistung unter einem Achskreuzwinkel dienen, erhöht werden kann. Hierzu untersuchte Mazak nicht nur wie üblich das Ausmaß des Verschleißes der Werkzeuge, sondern auch die erzielbare Werkstückqualität. „Bislang werden die Prozessparameter, die den Verschleiß möglichst lange herauszögern sollen, nach subjektiven Erfahrungswerten eingestellt“, berichtet die Preisträgerin. „Nun erhalten Hersteller klare Vorgaben für Parameter wie Werkzeugwinkel oder auch Art des Werkzeug-Vorschubs an die Hand.“ In den Versuchen konnte die Einsatzdauer um bis zu 12 Prozent gesteigert werden.
Kegelräder sind unter anderem in jedem Differenzial in Pkw und Lkw zu finden und sorgen für ein geschmeidiges Um-die-Kurve-Fahren. Doch wenige kennen sich mit diesen komplizierten Werkstücken wirklich aus. „Kegelräder sind sehr anspruchsvolle Werkstücke, man muss dreidimensional denken. Während meines Studiums konnten mir nur wenige erläutern, was es mit ihnen auf sich hat“, erinnert sich Julia Mazak. „Gerade dieses Mysterium hat mich sehr gereizt.“
Großbrand zerstört komplette Anlage
Vorversuche hatten gezeigt, dass der Werkzeugwinkel Einfluss auf seinen Verschleiß hat. Die junge Frau „leckte Blut“ und entschied sich 2015, ihre Doktorarbeit zu diesem Thema zu verfassen. Dass es ein Jahr länger dauern würde wie üblich, ahnte sie damals noch nicht. Im Jahr 2016 brannte die Versuchshalle der RWTH Aachen in einer Nacht bis auf ihre Grundmauern ab. Fast alle Verzahnungsmaschinen und auch Werkzeuge und Werkstücke fielen dem Feuer zum Opfer. „Doch die Firma Kordel Antriebstechnik aus Dülmen war so hilfsbereit, die Zerspanversuche in ihren laufenden Betrieb mit aufzunehmen. Dafür bin ich sehr dankbar“, betont Mazak mehrfach. „Ohne sie hätte ich nicht weitermachen können.“ Trotzdem hatte die Ingenieurin mit erschwerten Bedingungen zu kämpfen. Sie musste mehrfach zur Firma Kordel reisen, denn die Maschinen standen natürlich nur in bestimmten Zeitfenstern zur Verfügung. Das wiederum bedeutete nicht selten auch Nachtarbeit. Von ihrem Ziel ließ sich die 30-Jährige dadurch nicht abbringen.
Winkel vor allem im Kopfbereich von Einfluss
Am Werkzeug gibt es unterschiedliche Bereiche, deren Winkel theoretisch Einfluss auf die Geschwindigkeit des Verschleißes haben könnten. Mazak untersuchte die Hauptschneide, die aus Flanke und Kopf besteht. Sie konnte zeigen, dass der Winkel am Kopf kaum Einfluss auf den Verschleiß der Schneide hat. Anders die so genannten Span- und Freiwinkel an der Flanke der Schneide. „Wir haben uns in unseren Zerspanversuchen deswegen auf die Flanke konzentriert und den optimalen Winkelbereich definiert“, berichtet Mazak. „Hersteller können auf diese Empfehlungswerte ab sofort zugreifen und damit die Wirtschaftlichkeit ihrer Produktion deutlich erhöhen.“ Da die Werkzeuge bis auf wenige Mikrometer genau ausgerichtet werden müssen, ist der Einbau sehr aufwändig. Um den Verschleiß zu messen, müssen sie jedoch ausgebaut werden. „Wir haben nun erstmals Abdrücke von den Schneiden gemacht, und daran die Verschleißmarken gemessen. Das hat gerade einmal 3 bis 5 Minuten gedauert.“
Vorschub des Werkzeugs ebenfalls entscheidend
Es zeigte sich darüber hinaus, dass die Art des Werkzeugvorschubs ebenfalls Einfluss darauf hat, wie lange ein Werkzeug in der Maschine verbleiben kann. „Bei degressiven Vorschubrampen, bei denen das Werkzeug zunächst schneller und gegen Ende der Bearbeitung langsamer bewegt wird, hält es am längsten“, präzisiert Mazak. Um diese unterschiedlichen Zerspanungsbedingungen unter die Lupe zu nehmen, nutzte Mazak eine weitere innovative Methode. Mit so genannten Heatmaps konnte sie nachvollziehen, wie häufig während des Prozesses bestimmte Kennwerte am Werkzeug vorkommen. Das wiederum gibt Aufschluss darüber, wie stark ein Werkzeug belastet ist – das heißt, wie schnell es an welcher Stelle verschleißt. Heatmaps sind bekannt aus dem Fußball. Sie zeigen auf, welcher Spieler wie oft über das Feld gelaufen ist.
Autorin: Gerda Kneifel, VDW
Umfang: 4.128 Zeichen inkl. Leerzeichen
Ansprechpartnerin
VDW Verein Deutscher Werkzeugmaschinenfabriken
Gerda Kneifel
Presse- und Öffentlichkeitsarbeit
Corneliusstraße 4
60325 Frankfurt am Main
Deutschland
Tel. +49 69 756081-32