EMO Hannover TRENDSPOTS — Discover the product innovations of the world of metalworking: No. 4
Solutions with the moves!
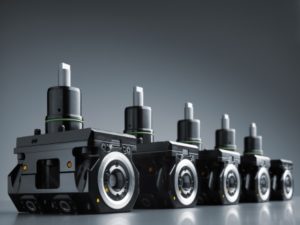
ALPHA LASER and Picum have announced a collaboration that meets a long-held industry desire for an end-to-end mobile laser welding and milling solution, without any need to transport components.
Rapid mobile servicing of tools, molds and other components and making changes to them represents a major customer benefit. Mobile laser welding machines located directly on-site can shorten the process chain considerably, as they eliminate time-consuming transportation of often cumbersome workpieces. Yet welding alone isn’t usually enough. Generally speaking, workpieces need further machining. This has so far been the job of stationary milling machines, whose work first has to be planned and scheduled by experts, involving major outlay, before the actual machining can start. And, as a result, the resource-saving on-site idea is no longer feasible. That, at least, has been the case until now. In the run-up to EMO Hannover 2019, ALPHA LASER GmbH, a specialist in developing and manufacturing laser systems, and the startup Picum MT have announced they are working together on mobile laser welding and milling – in other words, complete machining on-site.
Picum’s mobile milling machine makes this a reality. Weighing just 150 kilograms, it can be easily mounted on or next to a component and then performs machining operations fully automatically. After initial setup, the machine determines the component’s position and orientation and automatically generates the required machining code. The accuracy of this solution is said to be more than a match for stationary milling machines. Even complex free-form surfaces can be produced in virtually all materials on-site, thanks to five-axis simultaneous machining. An integrated measuring system also enables on-site quality assurance for the finished geometry. That’s why at EMO Hannover, ALPHA LASER isn’t just showcasing its own ALFlak 900 F laser system for repair welding using wire or powder but also the Picum solution for mobile milling.
ALPHA LASER GmbH (82178 Puchheim, Germany), Hall 16, Stand F22
Contact: Claudia Thornton
Tel.: +49 89 890237–113
Crème de la crème
TECNO.team is ensuring all eyes are on its stand at EMO Hannover 2019 with impressive productivity champions, bestsellers and two world grinding firsts.
As a renowned specialist in grinding and milling machines, and boasting decades of experience in high-precision finishing, TECNO.team GmbH has deliberately chosen only the best grinding and milling machines from European and Japanese market and technology leaders to enhance its product portfolio. The company is now seizing the opportunity at EMO Hannover 2019 to showcase a wide range of exhibits and innovations.
Pride of place goes to the two premieres from Curtis Machine Tools (CMT). “The two world firsts from CMT enable users to reach new heights in productivity,” says TECNO.team product manager Michael Blank. CMT has simply doubled the number of spindles. Vector Quad is fitted with four spindles, while Victor Pendulum features two workpiece spindles. This is set to boost productivity when grinding large series of small parts to unprecedented levels. At the same time, the chip-to-chip time has decreased, as setup can be performed in parallel with the machining operations and because loading can be carried out automatically.
Visitors to Hannover can also explore the GPH, a mainstay of the portfolio at SHIGIYA, Japan’s number one in cylindrical grinding. Meanwhile, MICRON, the country’s leading supplier of centerless grinding solutions, is showing off its MSL – a highly productive machine for through-feed grinding. Finally, two innovative solutions for coolants from BIX and Innogrind round off TECNO.team’s showcase of innovations.
TECNO.team GmbH (72138 Kirchentellinsfurt, Germany), Hall 11, Stand D62
Contact: Kirstin Danker
Tel.: +49 7121 68085631
Weight loss par excellence (and material savings)
Visitors to the Autodesk stand at this year’s EMO Hannover can discover how to use intelligent production technologies to optimize the entire process from design through to production. In particular, the company is turning the spotlight onto the untapped potential of generative design.
Generative design is a relatively recent approach to design that involves creating a broad range of possible solutions in a short space of time. Thanks to the high-performance capabilities and speed of modern cloud technology, generative design software can examine all the geometrical possibilities and then return a wide selection of options – all based on the materials, production processes and performance requirements stipulated for the object in question. Designers and engineers using this approach can very quickly establish an overview of different potential solutions to a specific design issue and then choose the solution that best suits their project. All in all, the process saves time, money and resources. This innovative approach is also part and parcel of Fusion 360, a product development platform that combines design, engineering and production in a single software package – and which Munich-based Autodesk GmbH is exhibiting at this year’s EMO Hannover.
One of the projects on show at the fair that demonstrates the Autodesk approach to design is the electric version of the well-loved VW transporter, known as Bulli in Germany. During this project, several components from the particularly popular Type 2 model of the transporter were optimized in a technical design environment before being produced. The designers were able to reduce the amount of materials used and thus achieve significant weight savings, which in turn have reduced the vehicle’s power consumption and increased its range. “The less a vehicle weighs, the less energy it takes to get it moving on the road,” explains Karl Osti, Industry Manager Manufacturing at Autodesk. “This is precisely where generative design can deliver huge benefits. It gives us the option to minimize material consumption and therefore manufacture lighter parts, all while ensuring technical requirements are met and without compromising stability.”
Autodesk GmbH (81379 Munich, Germany), Hall 9, Stand D24
Contact: Tom Rutteman
Tel.: +49 89 54769–0
Sparks are most certainly flying
Zimmer & Kreim GmbH & Co. KG has completely overhauled its die erosion technology and is exhibiting the end result – the genius 900 NOVA – at EMO Hannover 2019.
Zimmer & Kreim (ZK) has more than 30 years of experience in engineering cavity-sinking machines. Its genius range enjoys a particularly strong position on the market and has been continuously developed and improved over the years. Recently, however, the company decided to reconsider its approach – should it continue to tweak the technology, or break the mold? That’s how the company’s founder, Klaus Kreim, recalls the beginnings of the “genius 900 NOVA”, a die erosion machine that has been completely redeveloped from the ground up and is being exhibited for the first time at EMO Hannover 2019.
Although the company’s in-house generator technology and the 5th generation of its control system are still the beating heart of all ZK machines, virtually no other stone has been left unturned. For example, the substructure of the machine is no longer made of gray cast iron, but of thermo-symmetric mineral casting instead. This increases the weight of the machine base, which results in even faster axis movements and more accurate circular motions. The drive of the controlled C axis and the position of the coupling have also been modified. The aim was to gear the machine’s power and performance toward the profile of a high-end machine. “We have set out to build the best machine in its class,” says Armand Bayer, Managing Director of Zimmer & Kreim, describing the project. The previous genius user interface has also been completely overhauled to account for groundbreaking human-machine interfaces. It now offers systematic, intuitive user guidance on a Windows 10-based touchscreen with an aspect ratio of 16:9. What’s more, the machine has even more innovations to offer. If all that sounds appealing, then a visit to EMO Hannover 2019 is highly recommended. After all, why pass up on the chance to scrutinize the brand new solution in detail and put its capabilities to the test live?
Zimmer & Kreim GmbH & Co. KG (64395 Brensbach, Germany),
Hall 13, Stand B94
Contact: Michael Huth
Tel.: +49 6161 9307–0
A real looker!
Austrian measurement technology supplier Bruker Alicona is at EMO Hannover 2019 with an optical coordinate measuring system designed to provide optimum support for automatically placing and measuring components and sorting them into OK / not OK parts.
Enhancing measurement systems with collaborative robots to create the cornerstone of an automated quality assurance system is nothing new for Bruker Alicona. What is a first, however, is the pick & place solution the company has developed by combining the µCMM optical coordinate measuring system with a collaborative robot arm – and this innovation is on show at EMO Hannover 2019. Visitors to the fair can see the exhibit in action for themselves.
The component being inspected live in Hannover using the coordinate measuring system is a tried-and-tested customer application from an industrial quality assurance background. Bruker Alicona has partnered with Stepper, one of Germany’s leading lights in high-performance punching tools, to demonstrate the automated measurement of 3‑up stamping inserts. Only a single optical sensor is used to measure the position, shape and roughness of the tool. The stamping insert is found in stamping tools used to manufacture automotive contacts, among other things. Stepper manufactures up to 2,550 contacts every minute, which equates to three billion parts over just a few years. “Dimensional accuracy, surface quality and the position of the embossing die relative to the outer contour are the most important factors for stamping inserts,” explains Marcel Heisler, Head of Laser Ablation and High-Speed Cutting at Stepper. “Thanks to Bruker Alicona, I can cover all that with just one sensor.”
The µCMM optical coordinate measuring system is designed to provide the ideal solution in a whole variety of ways. The system exhibits excellent precision, even for shapes with tolerances measured in the single-digit µm range, and also ensures users benefit from efficient user guidance that has been designed so it can be used by several different operators. Stepper, which uses optical measuring technology as standard in quality assurance, believes the use of an optical coordinate measuring system ought to lead, first and foremost, to a clear reduction in measurement times. One crucial condition, according to the company, is that there should be no need to scan the entire component in order to check the relevant geometries with high precision. “We only measure the areas of the outer contour we really need to,” explains Heisler. “This reduces measurement times by more than two thirds.”
Alicona Imaging GmbH (8074 Raaba-Graz, Austria), Hall 6, Stand E39
Contact: Astrid Krenn
Tel.: +43 316 40 30 10 742
Bearing up in tight spaces!
HIWIN is setting out to make a big impression at EMO Hannover 2019 with the compact and exceptionally rigid crossed roller bearings of its CRB range. The space-saving solutions have been designed specifically to help engineers working on robots, machine tools and other automation systems.
HIWIN GmbH has specialized in developing, manufacturing and distributing linear technology for more than 25 years. Besides linear guideways, its product portfolio also includes ballscrews, linear actuators and ball bearings, not to mention complete positioning systems that incorporate linear motor axes, linear modules, planar motors, torque motors, position measurement systems, rotary tables and industrial robots. HIWIN manufactures both standard solutions and special customer-specific designs, and its service team offers consulting and product training, in addition to a maintenance and repair service. Among the company’s customers are individual users and OEMs from numerous and varied branches of industry, such as machine tool manufacturers and businesses that manufacture packaging machinery, specialist machinery and medical technology. The HIWIN exhibits at EMO Hannover 2019 include a solution for engineers who repeatedly come up against the same challenge when developing robots, rotary tables, machine tools and many other automation systems – how to integrate precise and rigid bearings into an incredibly tight space.
According to HIWIN, this is one challenge that nobody need fear now – thanks to the crossed roller bearings of the CRB range. The crosswise arrangement of the rollers at an angle of 90 degrees means the bearings can accommodate axial forces from both directions, radial forces, overturning torque loads and any combination of these. The secret to their high load-bearing capacity becomes clear on looking inside the bearings. Thanks to their special geometry, the spacers between the rollers need very little room, which means more rolling elements can be incorporated into the bearing than is the case with similar models. The special shape of the spacers also minimizes the points of contact with the rollers, thereby reducing friction losses to a minimum. The end result is a clear advantage over angular contact ball bearings and designs that use two bearing points – the HIWIN crossed roller bearings are much more compact and can therefore be used in the tightest of installation spaces. What’s more, the HIWIN crossed roller bearings score highly when it comes to rigidity, too. According to the manufacturer, the linear contact of the rolling elements makes the bearings three times more rigid than conventional ball bearings. The company offers five different designs of crossed roller bearing, two preload classes and three accuracy classes and supplies the bearings with or without optional sealing. In short, it has the right variant for pretty much any application.
HIWIN GmbH (77654 Offenburg, Germany), Hall 8, Stand A20
Contact: Werner Mäurer
Tel.: +49 781 93278–0
See what’s really what!
vectorcam GmbH is exhibiting a whole load of innovations from the latest version of its vectorcam software at EMO Hannover 2019. It aims to show how its customers can make their production even more efficient by directly machining a 3D model and utilizing the NC-Features Groove Milling and Circular Pocket.
NC-Features are designed to open up a wide range of functions for users and include impressive features such as exceptionally straightforward handling, optimum ease of use and a high level of safety in programming. According to the company, both simple and complex workpieces can be created with ease and dramatically reduce run times. Machining, which takes place directly on the 3D model, facilitates the automatic adoption of geometry data. Intelligent machining strategies enable short tool paths, and vectorcam automatically recognizes model features and shapes such as grooves, slots, drilled holes, contours and curves.
What’s more, machining processes that are repeated frequently are immediately saved and can also be called up and edited as often as necessary. Meanwhile, the integrated collision check safeguards tools, materials and machines. “Workpieces are becoming more complex and processing times are getting shorter, which makes smooth, flexible and cost-effective machining processes essential.” explains Günter Böhning, Managing Director of vectorcam GmbH. “We provide the perfect solution – innovative CNC software that is not only easy to handle and easy to learn but also uses the freshest technologies in the area of CNC programming. Through our CAD/CAM system, we help our customers get ahead – and we’ve been doing that for more than 25 years!”
vectorcam GmbH (33100 Paderborn, Germany), Hall 9, Stand A23
Contact: Lisa Nonnenmacher
Tel.: +49 5251 180 80 16
Tools at the cutting edge
Machine tool manufacturer CERATIZIT is using its expertise to develop special tools for electric motor production. This Luxembourg-based company is now unveiling two innovations at EMO Hannover designed for cost-effective and reliable use on large-series involving complex stator bores.
CERATIZIT, a privately owned company headquartered in Luxembourg, has been a pioneer in sophisticated hard material cutting and wear protection solutions for over 95 years. It develops and manufactures highly specialized cutting tools, indexable inserts and carbide rods. Indeed, the company is the world market leader in various application areas for wear parts. It is also successfully developing new carbide, cermet and ceramic grades for the wood and stone working industries, for example. At EMO Hannover 2019, the world’s premier trade fair for the metalworking sector, CERATIZIT is showcasing two complete new developments that are ideal for the cost-effective and reliable series processing of complex stator bores.
Stators, the rigid counterparts of rotors in electric motors, for instance, are playing a key role in the increasing shift toward e‑mobility. As stator bores generally have a diameter of over 200 millimeters, CERATIZIT’s tool developers had to pay particular attention to the boring tool’s weight. Thanks to ingenious designs and additive manufacturing processes, the company has now succeeded in going well below the standard minimum on the market, which means the multi-blade boring bars can also be used on CNC machining centers. What’s more, CERATIZIT offers useful add-ons such as digital fine adjustment and service life monitoring that are designed to increase process reliability.
CERATIZIT Deutschland GmbH (87435 Kempten, Germany), Hall 5, Stand B70
Contact: Norbert Stattler
Tel.: +49 831 57010–3405
Mobile: +49 170 448 36 43
A colleague of few words but many talents
Industrie-Partner has developed Robo Operator to help out when staff shortages loom and is unveiling its state-of-the-art solution at EMO Hannover 2019.
Many parts manufacturers, particularly SMEs, continue to use CNC machine tools that cannot be automated or are not configured for automation. These tools need at least one skilled employee to operate and monitor them at all times, which means the tools are idle when the employee is not present. If there is a shortage of skilled staff due to annual leave, sickness, parental leave or urgent orders, it is often difficult, or impossible, for companies to adapt their capacity. Industrie-Partner, an innovative and customer-focused supplier of mechanical engineering solutions, is at EMO Hannover 2019 to unveil Robo Operator, which aims to help out when staff shortages loom.
Robo Operator is designed to be a mobile and flexible automation solution that can be used to run virtually any CNC machine tool independently. Thanks to the minimal preparation, setup and programming involved, Robo Operator can be started up in next to no time, even by staff with no programming experience. The robot is then instantly able to take on the third shift or weekend work completely autonomously, thus also significantly improving machine tool productivity.
Prospective users can check out the benefits of Robo Operator for themselves on a completely risk-free basis by simply renting the robot from Industrie-Partner’s subsidiary EquipmentRental for a short time. Industrie-Partner points out that any problems can generally be resolved quickly and easily by a member of the service team, who can access the robot directly via the cloud. What’s more, thanks to AI and machine learning, Robo Operator “notes” the troubleshooting strategy so that it can use it autonomously for future issues.
Industrie-Partner GmbH (01640 Coswig, Germany), Hall 6, Stand J15
Contact: Ulrike Polnick
Tel.: +49 352 3831–0
True blue system
Alongside a series of process control solutions for the smart factory, Renishaw is also at EMO Hannover 2019 to unveil the new NC4+ Blue system, designed to ensure greater precision in non-contact tool setting thanks to a blue laser.
UK-based Renishaw is a global engineering and technology company with expertise in precision measurement and healthcare equipment. The company supplies products and services for a wide range of applications, from jet engine and wind turbine manufacture to dentistry and brain surgery. Its German branch is at EMO Hannover 2019 to present Renishaw’s latest solution for non-contact tool setting.
The new NC4+ Blue system is the latest version of Renishaw’s non-contact tool setting system. It is said to offer much greater precision in tool measurement than the existing NC4 series, with tool-to-tool performance proven to industry standards. NC4+ Blue features blue laser technology – an industry first – and enhanced optics. These two elements are set to deliver much greater accuracy in tool setting, which means workpieces can be machined more accurately and efficiently. Compared to the red laser sources used in most non-contact tool setting systems, blue laser technology has a shorter wavelength, resulting in improved diffraction effects and optimized laser beam geometry. This makes it possible to measure even very small tools accurately, while also reportedly minimizing tool-to-tool measurement errors.
Renishaw GmbH (D‑72124 Pliezhausen), Hall 6, Stand D48
Contact: Risshu Bergmann
Tel.: +49 7127 9811404
For photos and video clips, visit: Trendspots — Product Innovations
Categories: Allgemein