EMO Hannover TRENDSPOTS – Discover the product innovations of the world of metalworking: No. 1
We’ve got Industry 4.0 under control
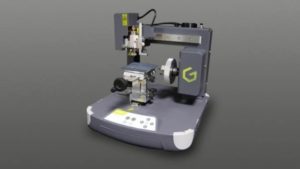
Automation, robotics and digitization with the Heronius SmartFactory – under the banner of “Innovation made in Germany”, Heronius is making its very first appearance at EMO Hannover in September 2019 to show visitors how they can control automation systems without a PLC.
The dynamic, new start-up Heronius GmbH divides its operations into three areas – digitization, automation and software development. The company is very clear about its goal – to use state-of-the-art technologies to bring the digitization of production facilities into the age of Industry 4.0 under the headlines Heronius SmartFactory and Heronius 360°. The start-up recently announced its participation in the German Machine Tool Builders’ Association (VDW) pavilion at EMO Hannover 2019 to showcase the fruits of its labor under the banner of “Innovation made in Germany”.
With the aid of the Heronius SmartFactory and the end-to-end system solution Heronius 360°, it seems it will soon be possible to control automation systems without a PLC (programmable logic controller). The systems are said to be designed in a way that enables completely intuitive setup. In fact, thanks to SmartFactory, users no longer require programming skills to configure even complex control sequences combining several components, such as robots, a machine, peripherals, sensors and actuators. Not only that, but the entire system was developed as a manufacturer-, product- and controller-independent solution from the very outset.
Heronius GmbH (73037 Göppingen, Germany), Hall 9, German Machine Tool Builders’ Association (VDW) pavilion
Contact: Christian Reik
Tel.: +49 7161 3540748
Solutions set to make their mark on industry!
Gravotech GmbH is bringing its extensive range of engraving and laser solutions, and dot peen marking systems to EMO Hannover.
The Gravotech Group is one of the world’s leading developers, manufacturers and suppliers of innovative engraving, marking and design modeling solutions. It is dedicated to providing a diverse portfolio of key technologies (laser marking, engraving, scribing and dot peen) and enhancing them with a wide range of materials and software solutions. Employing a workforce over 900-strong, Gravotech is represented in more than 100 countries worldwide. Its global network of 25 subsidiaries and 300 distributors works with over 60,000 customers all over the world, helping them overcome their day-to-day challenges.
Exhibiting in Hall 11, the group is showcasing laser markers for all marking and traceability applications from its flagship brands Gravograph and Technifor. The new LS900 Edge has been designed to mark and cut to size individual pieces and small to medium-size batches – all on a single machine. The group is also bringing its professional CO2 laser engraving and cutting systems, the LS100 and LS100Ex, to Hannover to wow trade fair visitors with their exceptional versatility. Equipped with a practical extraction system in the machine base, the LS100 and LS100Ex laser markers are also built to be extremely reliable and robust, while also meeting all the group’s high quality requirements.
What sets the M20 V3 apart from other systems is its extensive arsenal of tools and accessories that make it easy to apply diamond drag engravings and deep engravings to a wide range of materials, and cut fine workpieces to size. The machine sports a compact design so it can be set up in a store or small workshop without any problem. Weighing just twelve kilograms, it is also very easy to transport – for demonstration purposes, for example.
The new IMPACT dot peen marking system is said to be particularly suitable for the permanent series marking of small workpieces and small series of parts. According to Gravotech, texts, logos and Data Matrix codes can be engraved onto any shape, material or surface with a hardness of 62 HRC or lower. Meanwhile, the compact laser markers of the F series are designed to be easily integrated into the production sequence. Their extremely robust construction and high-end optics have been crafted to deliver outstanding stability, while also keeping maintenance outlay to a minimum.
GravoTech GmbH (79224 Umkirch, Germany), Hall 11, Stand F83
Contact: Astrid Stiefvater
Tel.: +49 7665 5007-16
Lathes are taking an intelligent turn
Companies will soon be able to integrate lathes manufactured by DMT into commonly used monitoring systems thanks to the specialist’s latest innovation – “Module 4.0” – debuting at EMO Hannover 2019.
End-to-end networking is crucial to smart factories and the intelligent machines operating within them. Companies rely on this feature to continuously monitor their production processes, enabling them to identify issues such as potential system damage early on and thereby avoid costly downtimes. With its new “Module 4.0”, DMT Drehmaschinen GmbH & Co. KG has developed a solution for integrating its lathes into intelligent production processes as the perfect companion to the “FZM18” remote access unit released just last year. The new “Module 4.0” is making its debut at EMO Hannover, where the company will also be accepting the first pre-orders for lathes equipped with this innovation (scheduled for shipping from December 2019).
“As state-of-the-art production chains are becoming increasingly digitized, many of our customers would like our lathes to feature enhanced connectivity to make them easier to integrate into their production control infrastructures,” explains Peter Walter, Head of Sales at DMT Drehmaschinen GmbH & Co. KG. “At the same time, however, they also want more information and diagnostic capabilities regarding the machine status so as to fully harness networking potential and optimize process steps.” By developing the new “Module 4.0”, DMT is committed to fully meeting these demands, as this solution comes with an additional function that checks the systems’ current operating status, thus offering an end-to-end interface solution for smart applications in DMT lathes.
DMT Drehmaschinen GmbH & Co. KG (79539 Lörrach, Germany),
Hall 26, Stand B01
Contact: Peter Walter
Tel.: +49 7621 9314-18
When 6×6 makes 102
Mikron Machining is at EMO Hannover 2019 to unveil the groundbreaking Mikron 6×6 modular machine tool building platform. This customizable system is available in 102 different combinations, ensuring it can be configured perfectly for any production scenario.
Part of the Swiss Mikron Group, Mikron Machining is a leading supplier of customer-specific, high-performance machining systems for manufacturing complex, high-precision metal components such as turbocharger housings, injection nozzles and ballpoint pen tips. To date, Mikron Machining has developed and commissioned over 7,000 machining systems. Its international customers include companies from the automotive, electronics, telecommunications, medtech, consumer goods, construction, pneumatics and hydraulics industries. One of the latest and already highly successful developments by Mikron Machining is the new Mikron 6×6 modular machine tool building platform, which the company is premiering at EMO Hannover 2019.
The Mikron 6×6 modular machine tool building platform offers no fewer than 102 different combinations. These result from six different workpiece tables, six automation variants, single- and dual-spindle machine versions and multi-clamping options. As each of the two spindles can reach all workpieces in the system, single-spindle CNC-corrected finishing can also be carried out in multiple clamping scenarios, in addition to dual-spindle rough and finish machining. According to the manufacturer, the Mikron 6×6 is one of the best machine tools in its class thanks to its compact design and versatility. The company sees its machining center as ideal for a whole range of sectors when it comes to efficiently machining high-end components made from steel, cast iron or light metal with first-class precision and within the tightest of tolerances.
Mikron SA Agno (6982 Agno, Switzerland), Hall 17, Stand C67
Contact: Bruno Cathomen
Tel.: +41 91610 6111
Sparks are flying in the aerospace industry
Mandelli Sistemi S.p.A. is at EMO Hannover 2019 to showcase its compact machining center, the SPARK 1200, which is said to be an ideal solution for the aerospace industry thanks to its outstanding performance – particularly with materials that are extremely hard and difficult to machine.
The Italian machining specialist sees its latest innovation as a compact multitasking solution. Boasting outstanding dynamic and static stiffness in its electro-welded structure, high torques and rigidity in its rotary table and spindle, and powerful drives, the new SPARK 1200 compact machining center is ideally equipped to deal with the materials used in the aerospace industry that are difficult to machine. Visitors to EMO Hannover 2019 can take a look at the impressive features of the latest development to come from this long-established company for themselves in Hall 12.
To achieve high dynamic and static stiffness, Mandelli has fitted the new SPARK 1200 with gantry drives and oversized roller slides instead of traditional linear axes. This ensures the feed is barycentric, while also increasing speed and acceleration. What’s more, the rotary axes now feature direct or double-pinion drives to eliminate any reverse backlash. The SPARK 1200 does, however, retain the innovative fixed table structure that has come to characterize the SPARK series. As a result, the machine’s dynamics are not dependent on the weight of the workpiece, which supports flexibility and the integration of multi-process operations. These include turning operations, which Mandelli successfully introduced some years ago with two larger models in the SPARK range and has now implemented on a more compact machine for the very first time. Sporting a steel construction, the SPARK 1200 is said to exhibit twice the stiffness when compared to cast iron constructions with the same mass ratios. Following an in-depth FEM analysis, it was designed to feature a staggered slideway solution with a highly optimized mass/yield ratio. Mandelli claims to have paid particular attention to generally dampening machining vibrations by introducing modular hardware and software devices that reduce negative effects while also ensuring a high material removal rate.
Mandelli Sistemi S.p.A. (Gruppo Riello Sistemi) (29122 Piacenza (PC), Italy),
Hall 12, Stand D50
Contact: Marco Colombi
Tel.: +39 0523 54 85 48
Mobile: +39 347 42 64 034
Smart plastics for longer life
Cologne-based igus GmbH will be at EMO Hannover 2019 to demonstrate how machine tool manufacturers and customers can use smart machine components made from high-performance plastics to cut costs by taking maintenance to a whole new level.
The Industry 4.0 era calls for a rethink of traditional processes in quite a number of areas. One example is using predictive maintenance based on continuous condition monitoring rather than checking machine tools at fixed intervals. These tools then only need to undergo maintenance or be replaced when the system signals this is necessary. Comparing status data with target parameters on an ongoing basis also measurably reduces unscheduled stoppages and therefore downtime costs. igus GmbH has achieved these benefits by using smart plastics to develop various sensors and monitoring modules for everything from energy chains and cables to plain, linear and slewing ring bearings. Networking these products with the new igus communication module (icom.plus), which igus is soon to showcase at the upcoming EMO Hannover 2019, ensures direct integration into the customer’s own IT infrastructure – into production management systems such as SCADA and MES, for instance, or online into cloud solutions that are used throughout a company.
Once programmed with initial service life algorithms using igus online configurations, icom.plus can also be operated offline if the customer wishes. This gives users flexibility when it comes to decisions about how the module is connected, how its data is managed and how to balance run time maximization against IT security. As long as icom.plus is online, the service life data is continuously compared with the igus cloud to maximize machine run times and minimize the risk of a failure. The data in the cloud includes details of the ten billion energy chain and cable test cycles performed each year in the company’s own 3,800 square meter test laboratory. Based on this data, it is possible to predict with impressive accuracy how long a component such as an energy chain will work reliably in the respective machine tool application. Integrated isense components that factor in the current ambient conditions provide additional reassurance by continually updating the service life. Machine learning and AI produce extremely precise data that can be viewed on the machine control system’s screen. If users opt for online connection, a text message or e-mail is also sent to notify them of unexpected operating states and scheduled maintenance.
igus GmbH (51147 Cologne, Germany), Hall 8, Stand E01
Contact: Oliver Cyrus
Tel.: +49 2203 9649-459
Anchors aweigh!
The specialist in cement-bonded mineral casting used in mechanical engineering, durcrete GmbH, is at EMO Hannover 2019 to showcase not only its optimized anchors for the cost-effective transportation of machine beds, but also a clever additive aimed at simplifying the process of manufacturing these beds.
durcrete GmbH is highly renowned for its application-ready solutions using ultra-high performance concrete (UHPC) and cement-bonded mineral casting in the mechanical engineering sector. The company’s innovations are used in the machine beds of machine tools, testing tables and the bases of handling units, but also in safety barriers in the construction industry. Depending on the application’s requirements, the self-compacting concretes from durcrete GmbH can be produced free from any plastics, fibers or reinforcement. The company is attending EMO Hannover 2019 to showcase two clever new solutions for the world of metalworking.
Firstly, among the cutting-edge exhibits is the product range for transportation anchors in Nanodur concrete developed by Dyckerhoff GmbH in collaboration with the transportation anchor manufacturer Schröder-Neuenrade, which provides short, compact options with reduced edge distances and metric threads. Besides that, durcrete GmbH is presenting its innovative new additive NANODUR® Extract, developed by Dyckerhoff GmbH with the aim of simplifying the production of massive machine components, particularly outside Europe. The manufacturer simply needs to mix NANODUR® Extract with local cements and aggregates to produce ultra-high performance concrete (UHPC) even more easily and cost-effectively.
durcrete GmbH (65549 Limburg/Lahn, Germany), Hall 7, Stand A83
Contact: Bernhard Sagmeister
Tel.: +49 6431 5840-376
Manufacturing that all adds up
At EMO Hannover 2019, TRUMPF is using components and practice-based demonstrations to show how companies can benefit from laser metal fusion and laser metal deposition and integrate these two technologies into conventional production processes.
With around 20 years of experience in additive manufacturing, TRUMPF is a pioneer in the sector and one of only a few manufacturers worldwide to offer the two relevant laser technologies under one roof – powder bed-based laser metal fusion (LMF) and generative laser metal deposition (LMD). From medical technology, aerospace and tool and mold making to automotive engineering and R&D, it would be difficult to find an industry that does not stand to benefit from the many advantages of these processes. Visitors to EMO Hannover 2019 have the opportunity to see these benefits for themselves in versatile solutions throughout the entire process chain, ranging from the robust machinery – with the TruPrint 3000 in action – and digitization, right through to comprehensive services and consulting.
The TruPrint 3000, a universal medium-format machine, is also being used to demonstrate the new TruPrint Setup Wizard, designed to ensure even safer and easier machine handling. Meanwhile, the LMD process adapter of a TruLaser Cell 3000 is being showcased at the stand of machine tool manufacturer Okuma. The compact and high-precision TruLaser Cell 3000 5-axis laser machine doesn’t just weld and cut in two or three dimensions – its fast process adapter changes also make it ideal for LMD. From prototypes to large-scale automated series production, the TruLaser Cell 3000 promises customers cost-effective and high-quality laser processing.
TRUMPF Laser- und Systemtechnik GmbH (71254 Ditzingen, Germany), Hall 9, Stand K02
Contact: Ramona Hönl
Tel.: +49 7156 303-31251
Switzerland and the USA make a perfect pair at EMO Hannover!
The Swiss-based LNS Group is using EMO Hannover 2019 to showcase something very special to the European market – the products of ChipBLASTER, the US coolant systems specialist it recently took over.
It is no accident that LNS was established in Orvin. In fact, the Jura region of Switzerland is an important center of mechanical engineering and the birthplace of the hydraulic bar feeder system. Today, just under 50 years on, the globally operating LNS Group is a leading manufacturer of systems for bar feeding, air filtration, coolant management and chip management. And now it is bringing ChipBLASTER to EMO Hannover, along with a new range of high-pressure coolant systems.
Having taken over the US-based ChipBLASTER Inc. in October 2018, the LNS Group is now using its sales and service network to introduce the company to completely new sales markets in Europe and the rest of the world. European companies that have never before encountered ChipBLASTER’s market-leading coolant management systems now have the ideal opportunity to cast their eye over the range at EMO Hannover 2019. Gilbert Lile, CEO of the LNS Group, on the takeover: “ChipBLASTER is a market leader in the U.S. high-pressure coolant industry and is a natural fit for our machine tool peripheral product portfolio. We plan to leverage our global sales and service network to sell ChipBLASTER’s technologically advanced products on a worldwide basis. A common thread running through both companies is the goal of helping manufacturers optimize the efficiency of their machine tools to improve performance, productivity and profitability.”
LNS Sàrl (2534 Orvin, Switzerland), Hall 17, Stand D16
Contact: Gilbert Lile
Tel.: +41 32 3580200
For photos and video clips, visit: Trendspots – Product Innovations
Categories: Allgemein