EMO Hannover TRENDSPOTS – Discover the product innovations of the world of metalworking: No. 3
Pilot customer en route to EMO Hannover 2019
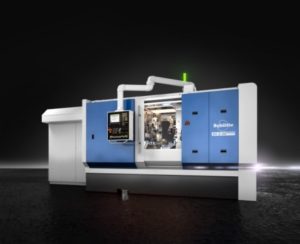
As a Siemens pilot customer, GEORG is attending EMO Hannover 2019 to unveil the digital twin for two of its machine tools, making it one of the world’s first manufacturers to have already taken the next concrete step in the digital transformation – with the new generation of CNC, Sinumerik ONE.
Until recently, the engineering of large machine tools would usually follow the same sequence. While the prototype was being developed and built, the software would be programmed at the same time – and the processes and workflows would only be brought together and optimized during commissioning. However, this approach is fundamentally changing with the advent of the “digital twin”. Using the next generation in CNC technology, Sinumerik ONE – which Siemens is unveiling to the public for the first time at EMO Hannover 2019 – all development processes can be mapped beforehand in a virtual environment. Siemens gives the following example: While a machine is still being manufactured, the control software is not only written, but also tested in a virtual world. At the same time, future users are trained on operator consoles that exactly match those of the machine that will ultimately be delivered.
As a specialist in machine tools and a pilot customer of Siemens, Heinrich GEORG GmbH has already implemented the digital twin in the form of Sinumerik ONE for two of its machines – the GEORG ultragrind SG2 grinding machine and the GEORG ultramill H moving column milling machine. The company aims to gradually offer further machine tools that feature this new control technology, which is geared toward digitization from the very outset. But GEORG is taking things one step further. Running high-capacity machines to process complex workpieces poses special control and operating demands, so the company has developed its own intuitive control system based on Sinumerik ONE – GEORG smartcontrol UG. With this system, the digital twin can be used for training and testing purposes – in combination with either the actual operator console or a virtual equivalent. Dr. Wieland Klein, CTO at GEORG, is certain the digital twin will deliver tremendous benefits for his customers: “The GEORG digital twin is key to the digital transformation of our machines. It allows us to simulate and test our customers’ operations in a completely virtual environment. Thanks to the interplay between the virtual and the physical machine combined with GEORG’s engineering know-how, our high-capacity machines and the new high-performance Sinumerik ONE software, our customers are sure to benefit from significant productivity gains in manufacturing. As a Siemens pilot customer, we are the first to offer applications based on this groundbreaking new system.”
Heinrich GEORG GmbH (57223 Kreuztal, Germany), Hall 13, Stand A64
Contact: Dr.-Ing. Uwe Stein
Tel.: +49 241 89468-55
Turning a market gap into a niche market
The Schütte Group has its sights set on the gap between traditional single-spindle machines and costly multi-spindle solutions. Its solution is its very first single-spindle automatic lathe, which is making its debut at EMO Hannover 2019 as part of the group’s new ECX series.
The Schütte Group is one of the world’s leading manufacturers of machine tools, particularly multi-spindle automatic lathes and 5-axis CNC grinding machines. The group’s newly developed ECX series offers a completely new system that promises potential customers optimum performance and maximum productivity, even for complex parts. The very first single-spindle automatic lathe in the company’s history combines the know-how and speed of the multi-spindle world with the user-friendliness of single-spindle machines. The innovative ECX series is now making its debut in an ideal setting – EMO Hannover 2019, the world’s premier trade fair for the metalworking sector.
Schütte aims to give users of its new machine concept the option of manufacturing smaller batch sizes at high rates of productivity, as sales manager Peter-Hans Schmidt explains. “This new machine is very versatile and can achieve performance levels between those of conventional single-spindle and multi-spindle automatic lathes,” he says of the strategy. “Our solution achieves significantly higher productivity levels than single-spindle machines, and we plan to grow our market share with customers that manufacture larger batch sizes.” For him, the underlying figures speak for themselves: A multi-spindle lathe costs about five times more than a single-spindle unit, but can also increase productivity sevenfold. The ECX bridges the wide gap between these two variants. “We anticipate a great deal of interest from the many companies that consider a multi-spindle machine too expensive, but can’t do everything they need to on a single-spindle machine. Now there’s finally a solution for them.”
Alfred H. Schütte GmbH & Co. KG Werkzeugmaschinenfabrik (51105, Cologne, Germany), Hall 17, Stand D08
Contact: Christoph Schiffer
Tel.: +49 221 8399-233
This group has a good grip on clamping technology!
The ROEMHELD Group is shining a spotlight on the digitalization and automation of manufacturing processes at EMO Hannover 2019, while also showcasing a whole host of new clamping solutions.
ROEMHELD, HILMA and STARK – the three brands of the Hesse-based ROEMHELD Group – are among the world’s market leaders for high-productivity solutions in industrial manufacturing, assembly, clamping and drive technology. The components, products and systems they offer promise, above all, to make production more efficient and more flexible. The ROEMHELD Group is putting digitization and automation center stage at this year’s EMO Hannover.
The company’s roster of innovations at the fair includes a range of clamping elements with integrated digital stroke measurement, fully electrical swing clamps in new sizes and the STARK.connect and STARK.airtec zero-point clamping elements with fully integrated sensors. What’s more, visitors can check out the trade fair debut of the first-ever STARK robot gripper with a zero-point clamping system that enables automated pallet changes, even on machine tables that don’t have their own hydraulic, pneumatic and electrical connections. Not only that, but the new pneumatic swing clamp, designed to maintain its clamping force even when pressure drops, can be seen for the first time in Hannover.
Römheld GmbH Friedrichshütte (35321 Laubach, Germany), Hall 4, Stand E54
Contact: Markus Isgro
Tel.: +49 716217 4658
I increase productivity, therefore I am!
Representatives from DP Technology are exhibiting a first in their company’s history at EMO Hannover 2019 – a new generation of machine-aware ESPRIT CAM software based on artificial intelligence (AI).
US-based DP Technology, which has a branch in the German city of Bamberg, is one of the leading manufacturers and suppliers of computer-aided manufacturing (CAM) software for a large section of the manufacturing industry. Indeed, the company’s main product – ESPRIT – is viewed as one of the most high-performance and high-quality NC programming systems for milling, drilling, turning and wire erosion machinery and is also used with multifunctional machinery such as mill turn centers.
Taking pride of place among DP Technology’s exhibits at EMO Hannover 2019 is the new “ESPRIT CAM system – powered by Artificial Intelligence”. As its name suggests, the algorithms of what is now the fourth generation of the software are based on artificial intelligence (AI). The new technology is designed to simplify programming processes and improve machine productivity on the shop floor. The patent-pending system is also machine-aware, drawing this awareness from a digital twin of the CNC machines, tooling and fixtures. According to DP Technology, these new advances are the result of 35 years of innovation and make this market launch the most exciting product rollout in the company’s history. “Our AI engine represents a fundamental change in the way CNC machines are driven,” says Chuck Mathews, Chief Technology Officer for ESPRIT’s parent company, DP Technology. “The new ESPRIT CAM system’s AI machine-aware algorithms provide an exceptional user experience – simplifying programming, increasing tool life and improving machine performance.”
DP Technology Germany GmbH (96052 Bamberg, Germany),
Hall 9, Stand D06
Contact: Theresa Höreth
Mobile: +49 175 849 33 94
Keeping things steady Swiss-style
EMO Hannover 2019 is to host yet another major product launch, as NUM AG exhibits its brand-new and innovative accelerometer-based active vibration control system for CNC machine tools.
Swiss-based NUM AG is used to being ahead of the game. In fact, by the time CNC and NC controls started to gradually spread in the early 1970s, the company already had a ten-year head-start on development work in the field. When it delivered its first marketable products, back in 1964, NUM was one of the first ever suppliers of CNC in the world. Since then, it has maintained its position as a technological pioneer in the field and also worked to extend its lead. All that hard work at NUM AG has produced a great many solutions, and one of the latest is an innovative, accelerometer-based active vibration control system. This system has been developed for CNC machine tools and is set to launch exclusively at EMO Hannover 2019.
Compared to previous alternatives, the active vibration control system is very cost-effective and is used primarily to virtually eliminate tool head vibration and thus improve machining. By maximizing the material removal rate, it increases productivity, while also providing valuable real-time feedback for predictive maintenance purposes. The innovative vibration control system from NUM is available as a retrofittable option for any machine tool that uses NUM’s MDLUX high-performance digital servo drives, which form part of the company’s Flexium+ CNC platform.
NUM AG (9053 Teufen, Switzerland), Hall 9, Stand E40
Contact: Peter von Rüti
Tel.: +41 71 335 04 11
EAsy dos it!
At EMO Hannover 2019, MAPAL Präzisionswerkzeuge Dr. Kress KG is showcasing its newly developed EA System, which is designed to make the process of adjusting external reamers for the fine machining of small outer diameters far easier.
Grinding is often used for the fine machining of small outer diameters, but external reaming provides a cost-effective and therefore attractive alternative. If an IT6 fit is required on a lathe for series production, for example, external reamers with an adjustable insert and guide pads can be relied upon to get the job done – provided the tool’s diameter and the insert’s back taper can be set with pinpoint accuracy. MAPAL Präzisionswerkzeuge Dr. Kress KG has chosen EMO Hannover 2019 to unveil a new system it has developed to make adjusting external reamers with small diameters far simpler.
In the EA System (EA = EasyAdjust), the back taper of the insert is already integrated into the cassette serving as the insert mounting. This completely eliminates the need to adjust the back taper of the minor cutting edge. Once the above-mentioned cassette has been removed, it is quick and easy to adjust the insert itself using a micrometer or measuring plate. The appropriate setting dimension for the insert is inscribed on the reverse of the tool. This corresponds exactly to the midpoint of the tolerance for the required fit. Thanks to an impressive changeover accuracy of two to three microns and the extremely straightforward adjustment of the insert, the new system now makes it much easier to comply reliably with the required tolerances and extremely precise fits, even in the case of small diameters. The EA System can be used with indexable inserts that have either four or six cutting edges.
MAPAL Präzisionswerkzeuge Dr. Kress KG (73431 Aalen, Germany),
Hall 4, Stand A18
Contact: Andreas Enzenbach
Tel.: +49 7361 585 3683
Machining on a grand scale
Mechanical engineering company LiCON is at EMO Hannover 2019 to exhibit the LiFLEX I 12126, its new and improved single-spindle machining center that boasts a unique combination of speed and cubic dimensions. The solution is said to be ideal for much larger machining dimensions, like those involved when working on structural components.
LiCON, the system supplier of production lines for the series machining of complex components, is showcasing a new version of its LiFLEX I 12126 single-spindle machining center at this year’s EMO Hannover. The improvements in the LiFLEX I 12126, which is designed primarily for work on structural components made of lightweight metal, means it can now machine even bigger dimensions than it could before. Depending on its configuration, the new machine can operate with four or five axes and is exceptionally fast, dynamic, stable and robust. What’s more, tools can be changed in just one second. With rapid traverse speeds of up to 150 meters per minute in the linear axes and high acceleration and jerk values, the machine is said to be one of the most dynamic for its cubic dimensions on the market.
“One example of an application is the machining of subframes for cars. It’s really important that this large component can be positioned in any way and that machining work can be performed at all the relevant points – if at all possible without having to also use angular heads. To safeguard the overall performance of the machine, we use only components from our own modular LiFLEX system,” explains Winfried Benz, Managing Director of LiCON.
LiCON mt GmbH & Co. KG (88471 Laupheim, Germany), Hall 12, Stand D66
Contact: Nils Baumgartner
Tel.: +49 7392 962186
Smooth operator
OTEC Präzisionsfinish GmbH, a specialist in perfect surfaces, is at EMO Hannover 2019 to showcase a range of items, including its newly updated CF Series disc finishing machine.
Since it was founded in 1996, OTEC Präzisionsfinish GmbH has grown from being a small manufacturer of polishing machines for the jewelry and watchmaking industry to become a global specialist in precision technology for achieving perfect surfaces. Whether it’s deburring, grinding, smoothing or polishing, OTEC machines deliver efficient surface finishing for tools and products in many different industries. At EMO Hannover 2019, OTEC is exhibiting a whole host of interesting exhibits, including the recently revamped CF Series disc finishing machine.
Thanks to its modular and compact design and optimized welded structure, the new CF Series machine has been built to ensure trouble-free operation and a long service life. It can be used wherever rapid surface treatment is needed for fine blanked, turned, milled and punched parts and jewelry. Besides the welded structure, OTEC has also optimized the waste water drain. What’s more, the machine now boasts a 7.5-inch color touch display that can be used to create and store up to 1,000 programs quickly and easily, making it even more efficient and user-friendly, according to the company. Options for remote machine maintenance and control are also integrated. In addition, the machine features storage space for a compound container and pumping station, and can be disassembled and reassembled quickly and easily for transportation.
OTEC Präzisionsfinish GmbH (75334 Straubenhardt, Germany),
Hall 11, Stand G56
Contact: Vivian Wasner
Tel.: +49 7082 4911-670
For photos and video clips, visit: Trendspots – Product Innovations
Categories: Allgemein