Ohne KI bald k.o.?
EMO Hannover 2019: Mit „Ingenieur-Denke“ systematisch künstliche Intelligenz einsetzen
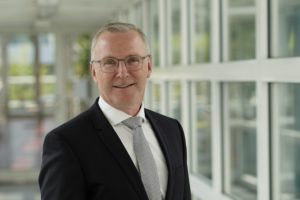
Frankfurt am Main, September 2019 – Die Überschrift provoziert – mit Absicht. Denn mit Blick auf China, Japan und USA, die laut einer Studie von Boston Consulting aus dem Jahr 2018 auf dem Gebiet künstliche Intelligenz (KI) schon lange kräftig aufrüsten, ist in Europa Aufwachen angesagt. Einen Weckruf startet daher Prof. Jörg Krüger, Leiter des Fachgebiets Industrielle Automatisierungstechnik, Institut für Werkzeugmaschinen und Fabrikbetrieb (IWF) der TU Berlin, und Bereichsleiter Automatisierungstechnik am Fraunhofer IPK. Der Tipp des KI-Pioniers für Produktioner: Lassen Sie sich auf der EMO Hannover 2019 von der WGP (Wissenschaftlichen Gesellschaft für Produktionstechnik) und mutigen Maschinenherstellern zu ersten KI-Schritten inspirieren.
Herr Professor Krüger, wie und wann hatten Sie Ihren ersten Kontakt zu KI?
Jörg Krüger: Das geschah 1992, als ich mich mit künstlichen neuronalen Netzen bei der Diagnose von Werkzeugmaschinenachsen beschäftigte. Heute bin ich fasziniert von den enormen Fortschritten durch Deep Learning (Teilbereich des Machine Learning, der neuronale Netze und große Datenmengen nutzt, Anm. des Autors) und Convolutional Neural Networks (laut Wikipedia ein von biologischen Prozessen inspiriertes Konzept im Bereich des maschinellen Lernens, Anm. des Autors), die zum Teil die menschlichen Fähigkeiten in der Muster- und Bilderkennung bei der Verarbeitung von Audio- und Videodaten bereits übertreffen.
Mit einfacheren Strukturen komplexe KI-Systeme beherrschen
Im November 2018 erschien im Münchner Riva-Verlag das Buch Der unterlegene Mensch: Digitalisieren wir uns mit Algorithmen, künstlicher Intelligenz und Robotern selbst weg?. Was halten Sie von den pessimistischen KI-Ansichten des Autors Prof. Armin Grunwald, der ja als Leiter des Büros für Technologiefolgen-Abschätzung beim Deutschen Bundestag (TAB) einen gewissen Einfluss besitzt?
Jörg Krüger: Ich verstehe seinen skeptischen Blick auf die teilweise Undurchschaubarkeit dieser Systeme, denn deren Komplexität nimmt weiter zu. Wir müssen einfachere Strukturen der Automatisierung schaffen, mit denen sich die Komplexität maschineller Lernverfahren besser verstehen und beherrschen lässt. Es geht darum, ob Produktioner einem lernenden System soweit vertrauen können, dass sie es in der Produktion „scharf schalten“. Weil sich Aus- und Weiterbildung aber oft nicht schnell genug an diese schnelle Entwicklung in der Forschung anpassen, gelingt es uns nur mit erheblicher Verzögerung, entsprechende Fähigkeiten zur Beherrschung der Komplexität aufzubauen und Vertrauen in diese neuen Technologien zu schaffen. Das alles schürt natürlich die Vorstellung, dass der Mensch irgendwann unterliegt.
Das Domänenwissen der Mitarbeiter anzapfen
Und dann steht der Produktioner vor einem Big Data-Gebirge: Wie geht er damit um?
Jörg Krüger: Es kommt sehr darauf an, um welche Art von Daten es sich handelt und welche Zielsetzung der Produktioner verfolgt. So ging es einem Anwender darum, per Bilderkennung 50.000 bis 60.000 Teile in einem Lager zu erkennen und zu verwalten. Bisher übernimmt ein Lagerarbeiter die Arbeit, bei der er die Teile anhand eines Kataloges identifiziert und sortiert. Wir ließen von jedem Teil nur eine begrenzte Anzahl von Aufnahmen machen, die zum Erfassen einer neuronalen Netzstruktur eigentlich nicht ausreichen. Doch wir stellten fest, dass sich mit vortrainierten Netzen auf Basis nichtindustrieller Bilddaten in Kombination mit wenigen industriellen Bauteildaten schon früh akzeptable Erkennungsquoten für Assistenzfunktionen erzielen lassen. Das KI-System arbeitet dann als halbautomatischer Assistent, der dem Lagerarbeiter jeweils die fünf wahrscheinlichsten Teile anzeigt. Dank dieser Assistenz arbeitet er nun deutlich effizienter und genauer. Das funktioniert aber nur, wenn man die Prozesse sehr genau kennt. Daher lautet meine Botschaft: Nicht nur in Hard- und Software investieren, sondern auch systematisch das so genannte Domänenwissen der Produktioner nutzen. Menschen müssen außerdem lernen, Vorgänge in der Fabrik zu bewerten und zu entscheiden, welche Aufgaben die KI übernimmt. Generell ist das Einbeziehen des Domänenwissens aus der Produktion elementar, um neue Wertschöpfungspotenziale schnell und systematisch zu identifizieren.
Daten sind digitaler Goldstaub
Clevere Assistenz ist ein Aspekt, was hat KI noch zu bieten?
Jörg Krüger: Die in den Firmen erzeugten Daten sind für mich digitaler Goldstaub. Viele Unternehmen sind sich aus meiner Erfahrung noch nicht bewusst, welche Wertschöpfungspotenziale sie damit erschließen können. Die Werkzeuge für das maschinelle Lernen werden immer leistungsfähiger. In der Produktion sollten wir nun systematisch die Daten und das Domänenwissen verbinden, um die Prozesse weiter zu verbessern und effizienter zu werden. Dieses Thema möchte ich mit den Kollegen der WGP forciert angehen. Wir sollten z.B. unseren Fokus nicht wie früher auf die Erhöhung der Erkennungsquoten mithilfe von maschinellen Lernverfahren richten, sondern einerseits systematischer als bisher die vorhandenen Produktionsdaten auf ihr Potenzial zum maschinellen Lernen analysieren und andererseits auch systematischer die daraus resultierenden Potenziale zur Effizienzsteigerung in der Produktion ableiten. Ich empfehle dazu das Youtube-Video des kanadischen Wissenschaftlers Ajay Agrawal beziehungsweise sein Buch Prediction Machines: The Simple Economics of Artificial Intelligence. Hier kann ein Automatisierer oder Produktioner die Chancen von KI aus der ökonomischen Perspektive kennenlernen, um den digitalen Goldstaub im eigenen Unternehmen zu entdecken. Es entstehen plötzlich völlig neue Wertschöpfungsmodelle und Nischen für kleine Unternehmen sowie vor allem für Start-ups.
Welche Rolle spielen Sensoren?
Jörg Krüger: Die „Sensorisierung“ ist in der Regel der erste Schritt, um Daten für das Lernen zu gewinnen. Je leistungsfähiger und günstiger die Werkzeuge für das maschinelle Lernen sind, umso wertvoller werden die Daten, mit denen dies geschieht. Gerade im Bereich der Sensorisierung sind ja durch die Forschung und Entwicklung in Bezug auf Industrie 4.0 große Fortschritte zu sehen – eine gute Voraussetzung, um jetzt den nächsten Schritt zum maschinellen Lernen in der Produktion zu machen.
Systematische KI-Lösungen dank deutscher „Ingenieur-Denke“
Doch wie sehen unsere Chancen aus gegenüber Ländern wie China, die ja enorme Beträge in KI stecken?
Jörg Krüger: Die Investitionen in KI-Infrastrukturen, die gerade aus China bekannt werden, sind in der Tat beeindruckend: kaum vorstellbar, hier aus Deutschland in der gleichen Dimension mithalten zu können. Im internationalen Wettbewerb sehe ich jedoch für Deutschland eine gute Zukunftschance darin, mit strukturierter Ingenieur-Denkweise an das Thema der industriellen Nutzung von KI bzw. dem maschinellen Lernen heranzugehen. In dieser Form sollten wir in Zukunft auch unsere weltweit sehr gute Position im Bereich der Automatisierung weiterentwickeln und erhalten können.
Was reizt Sie – nicht nur mit dem Blick des KI-Interessierten und forschenden Produktioners – besonders an der EMO Hannover 2019?
Jörg Krüger: Interessant werden sicher Exponate von WGP-Kollegen sein. So hörte ich von einem Institut, dass er etwas sehr Spannendes aus dem Bereich Mustererkennung an Werkzeugmaschinenantrieben ausstellen wird. Mehr darf ich nicht verraten. Ebenso dürfte sich eine Stippvisite zu manchen Maschinenherstellern und Automatisierungsunternehmen lohnen.
Herr Professor Krüger, wir danken Ihnen für das Gespräch.
Trumpf: KI-Einsatz in der Produktion
„Künstliche Intelligenz ist kein Job-Killer, sondern ein weiterer konsequenter Schritt, um die Wettbewerbsfähigkeit Deutschlands und den Wohlstand hier abzusichern“, sagt Dr. Thomas Schneider, Geschäftsführer Entwicklung des Geschäftsbereiches Werkzeugmaschinen der Trumpf GmbH + Co. KG, Ditzingen. „Unser über Jahrzehnte gesammeltes Wissen im Maschinenbau ist für den Einsatz von Künstlicher Intelligenz in der Industrie das A und O. Diese Chance müssen wir nutzen.“ Die Schwaben setzen KI bereits in die Tat um: 25 Mitarbeiter sorgen bei Trumpf bereits für die gruppenweite Abstimmung und Transparenz der Aktivitäten zu diesem Thema. So analysiert KI zum Beispiel in einem Laservollautomaten die zunächst missglückte, dann aber erfolgreiche Entnahme von geschnittenen Blechteilen und automatisiert die Vorgehensweise mit Hilfe der analysierten Daten. Die Methode kann Trumpf dann auf Maschinen dieses Typs übertragen. Bewährt hat sich KI auch in der eigenen Produktion: Sensoren in der Maschine erfassen bei einem kurzen Test große Mengen an Daten und senden sie über die Steuerung in die Cloud, in der die KI-Lösung sie automatisch analysiert. Eine geschickte Kombination aus Simulations-, Mess- und Analyseverfahren ermöglicht so die Überprüfung der Maschine in unzähligen Betriebszuständen. Stimmt in den Daten etwas nicht, erkennt sie nicht nur den Fehler, sondern durch ihre vorherigen Analysen auch, wie er sich beheben lässt.
Autor: Nikolaus Fecht, Journalist aus Gelsenkirchen
((Umfang: rund 8700 Zeichen inkl. Leerzeichen))
Neue Technologien beflügeln das Geschäft von morgen
EMO Hannover 2019 widmet Zukunftstechnologien eigenes Forum
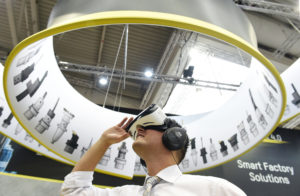
Frankfurt am Main, 09. September 2019. – Hinter dem Begriff Industrial Internet of Things (IIoT) stecken gleich eine ganze Reihe neuer Technologien, die der Produktion innovative Möglichkeiten eröffnen. Daraus sollen wiederum neue Geschäftsfelder entstehen. Auf der EMO Hannover 2019 wird der nicht zu unterschätzenden Bedeutung des IIoT mit dem Forum New Technologies – Future Opportunities Rechnung getragen. An fünf Tagen halten führende Experten aus Industrie und Wissenschaft in Halle 9 Vorträge zu Zukunftstechnologien, die sich zu wichtigen Säulen der Metallbearbeitung entwickeln werden. Die Teilnahme ist kostenlos, Vortragssprache ist Englisch.
Hinter dem Industrial Internet of Things stehen Schlagwörter wie additive Verfahren, Maschinelles Lernen und Künstliche Intelligenz, Plattformökonomie, umati, OPC UA und 5G. Doch was steckt wiederum hinter diesen omnipräsenten Begriffen? Und wie können diese Technologien die Wertschöpfung im produzierenden Gewerbe beflügeln?
Vernetzung ganz praktisch auf Maschinen- und Geschäftsebene
In einer vernetzten Welt ist ein gesicherter Weg zum Austausch standardisierter Daten und Informationen vom Sensor bis zum IT-Unternehmen der größte Vorteil, um die Engineering-Kosten zu senken und die Sicherheit zu erhöhen. Für den Datenaustausch hat der Markt das plattformunabhängige OPC UA als Standard für das OPC UA als Framework für industrielle Interoperabilität entschieden. Warum? Und wie kann man heute bestehende Maschinen anbinden, die ohne OPC UA geliefert werden? Das Forum gibt am Dienstagnachmittag einen Überblick über den Status quo und die Roadmap von OPC UA. Darüber hinaus zeigen erfahrene Unternehmer, wie Cybersicherheit und Assistenzsysteme den Weg zu einer erfolgreichen, sicheren und benutzerfreundlichen IIoT-Anwendung ebnen.
Die Wertschöpfung durch digitale Dienste wird auch ein Schlüsselelement zukünftiger Geschäftsmodelle sein – dessen sind sich die Experten einig. Sie werden Werkzeugmaschinenbauer in die Lage versetzen, den künftigen Anforderungen ihrer Kunden nachzukommen und sich im internationalen Wettbewerb zu behaupten. Ein Begriff, der diesbezüglich die Runde macht, ist die Plattformökonomie. Unternehmer, die bereits Erfahrungen gesammelt haben, berichten unter anderem über skalierbare digitale Plattformen und wie produzierende Unternehmen von Abonnement-Geschäftsmodellen profitieren können.
Konnektivität dank umati und 5G
Um die immensen Potenziale für die industrielle Produktion zu heben, muss Konnektivität nicht nur von Maschine zu Maschine, sondern über die gesamte Wertschöpfungskette hinweg möglich sein. Wie Industrie 4.0 und IIoT umfassende Realität in der deutschen Wirtschaft werden können, darüber referieren Experten internationaler Unternehmen Themen sind unter anderem die Leistungsfähigkeit von Daten und zuverlässige Funkkommunikation. Darüber hinaus informiert das Forum “5G. Make manufacturing smart.” speziell über 5G im industriellen Umfeld. Koordinator des Forums ist die “5G Alliance for Connected Industries and Automation”, kurz 5G-ACIA. Sie ist das zentrale globale Forum für die Gestaltung von 5G für industrielle Anwendungen.
Nicht zuletzt wird die universelle Werkzeugmaschinenschnittstelle umati Industrie 4.0 stark vorantreiben. Was als Initiative des VDW (Verband Deutscher Werkzeugmaschinenfabriken) begann, hat sich zu einer weltweit unterstützten Bewegung entwickelt, um eine einfache und sichere Verbindung zwischen Werkzeugmaschinen und IT-Systemen im Produktionsumfeld sicherzustellen. Auf dem Forum erfahren Zuhörer am Freitag technische Details zum Stand der Dinge, welche Möglichkeiten Unternehmen, die von Anfang an bei der Initiative mitgewirkt haben, in umati sehen und wie andere Unternehmen daran teilhaben können.
Über die Vorträge zur Konnektivität hinaus wird auf der EMO Hannover übrigens ein erster 5G-Showcase unter Beteiligung von Ericsson, Stockholm, Makino Europe, Hamburg, und dem Fraunhofer Institut für Produktionstechnologie (IPT) präsentiert werden. Basierend auf der 5G-Technologie wird ein Roboter auf einem eigens entwickelten fahrerlosen Transportsystem Werkzeuge aus einem Regal nehmen, diese vermessen und eine Maschine damit beladen. Der Datentransfer zwischen der zentralen Steuereinheit und dem Roboter ist extrem schnell, da er über 5G stattfindet. Besucher des Showcase können sich bei Makino in Halle 12, Stand B36 informieren, wie sie 5G-Prozesse in ihre Produktionsanlagen integrieren können.
Künstliche Intelligenz und 3D-Druck
Dass künstliche Intelligenz (KI) und dabei insbesondere das maschinelle Lernen (ML) auf dem Weg in die praktische Umsetzung ist, zeigen die Vorträge am Dienstagvormittag. Es geht um die Frage, wie Unternehmen ihre automatisierte Produktion um ML- beziehungsweise KI-Methoden ergänzen können. Hierzu stellen die Sprecher auch konkrete Beispiele vor, wie das Verhindern von Rattern
oder sprachgesteuerte KI-basierte Maschinenbediensysteme. Es werden außerdem eine praktische ML-Anwendung für Planung, Terminierung und Betriebsführung präsentiert.
Es dürfen natürlich auch Vorträge zu additiven Verfahren nicht fehlen, die bereits Einzug in die Metallbearbeitung gehalten haben, insbesondere in den Branchen Luft- und Raumfahrt sowie Medizintechnik. Durch die rasanten technischen Fortschritte als auch die Erforschung immer neue Materialien für den industriellen 3D-Druck werden sich weitere Anwendungsgebiete eröffnen. Doch wieweit können Unternehmer schon heute additive Verfahren in ihre Produktion integrieren? Welche Besonderheiten sind zu beachten? Das erfahren die Zuhörer am Mittwoch und Donnerstag.
Das offene Forum mit jeweils halbtägigen Themenblöcken findet in Halle 9, Stand I24 statt.
Autorin: Gerda Kneifel, VDW
Umfang: 4.128 Zeichen inkl. Leerzeichen
Leichtbau ist Schlüsseltechnologie für die globale Nachhaltigkeit
EMO Hannover 2019 zeigt: Nachhaltigkeit und Leichtbau sind im Maschinenbau fest verankert.
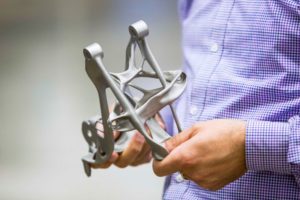
Photo: GM
Frankfurt am Main, September2019. – Intelligente Leichtbaulösungen fassen im Werkzeugmaschinenbau zunehmend Fuß. Dabei stehen neue Geometrien und Materialien genauso im Fokus wie die Simulation und der 3D-Druck. Wie Produkte im Kontext von Leichtbau und Nachhaltigkeit konzipiert und gefertigt werden können, zeigen die Aussteller der EMO Hannover an vielfältigen Beispielen.
Leichtbau ist elementarer Bestandteil für nachhaltiges Handeln. Er beginnt bereits weit vor der eigentlichen Herstellung und zieht sich durch die gesamte Wertschöpfungskette durch – vom Rohstoff bis zum fertigen Bauteil. Entsprechend frühzeitig setzen sich die Unternehmen mit diesem Thema auseinander. „Nachhaltigkeit ist ein zentraler Bestandteil unseres Unternehmens. Die Mission von Autodesk ist es, die Designentwürfe von Kunden zu automatisieren und Prozesse zu entwickeln, damit sie mehr und besser gestalten können – und das mit weniger negativen Auswirkungen auf die Umwelt. Mit Autodesk-Technologie können Hersteller ihr Ergebnis verbessern und dazu beitragen, eine bessere Welt zu gestalten, indem die Material- und Energieeffizienz in ihren Design- und Herstellungsprozessen gesteigert wird“, sagt Steffen Krause, Technical Sales Manager beim Softwareentwickler Autodesk.
Auch für Hainbuch, den schwäbischen Hersteller von Werkstückspannlösungen aus Marbach, ist Nachhaltigkeit und damit auch die Verpflichtung zur Umwelt selbstverständlich und ein wichtiges Element der Firmenidentität. So ist seit 2016 in den Umweltleitlinien eine Energie-Norm als sogenannte Energiepolitik verankert. „Damit reduzieren wir Emissionen und Abfälle, erhöhen die Energieeffizienz, garantieren den sparsamen Umgang mit Ressourcen und die Reduzierung gefährlicher Stoffe. Denn wir wollen die Produkte nicht nur qualitativ hochwertig entwickeln und produzieren, sondern auch umweltschonend und nachhaltig“, erklärt Stefan Nitsche, Leiter Produktmanagement bei Hainbuch.
Leichtbau ist eine wesentliche Voraussetzung für Materialeffizienz
Die 3D Micro Print GmbH aus Chemnitz ist spezialisiert auf die Herstellung von Mikrometallteilen durch Mikro-Lasersintern und den Verkauf der zugehörigen Maschinen. Für das sächsische Unternehmen bedeutet Nachhaltigkeit auch, Produkte mit Funktionsintegration zu entwickeln und herzustellen und so einen Mehrwert für die Kunden zu schaffen – ohne Einschränkungen bei den Materialeigenschaften und beim Produkteinsatz der Bauteile.
„Das Zusammenspiel zwischen neuen Geometrien und neuen Materialien ist essenziell, um mit Blick auf Leichtbau und Nachhaltigkeit Produkte mit einem Mehrwert zu generieren. An dieser Stelle bedarf es zudem einer fachgerechten Beratung, um dem Kunden die Stellschrauben für die Produktentwicklung und den Herstellprozess aufzuzeigen“, betont Thomas Klotz, Leiter der Qualitätssicherung bei 3D Micro Print.
Fest steht: Der 3D-Druck ermöglicht den Leichtbau und ist damit auch eine wesentliche Voraussetzung für Materialeffizienz. Mehrere Teile können dabei bereits im Design zu einer Komponente zusammengefügt werden. „Der Generative Design-Ansatz von Autodesk ist ein wichtiges Werkzeug, das oft neue geometrische Formen schafft. Es hilft unseren Kunden, Gewicht zu reduzieren und Teile zu konsolidieren. General Motors nutzte beispielsweise den Generativen Design-Ansatz von Autodesk und die additive Fertigung, um eine Sitzhalterung neu zu gestalten. Das neue Teil bestand aus einer, statt wie vorher aus acht Komponenten. Es war darüber hinaus 40 Prozent leichter und 20 Prozent stabiler”, nennt Krause ein Beispiel für ein Bauteil, welches von Beginn an konsequent unter Leichtbauaspekten entwickelt wurde.
Leichtere und kleinere Spannmittel verringern die Kosten je Werkstück
Hainbuch entwickelte für das Spannen von Werkstücken beim Fräsen, Drehen und Schleifen ultraleichte Spannmittel aus Carbon. Diese sorgen laut Unternehmen für eine höhere Produktivität, einen geringeren Energieverbrauch und eine Entlastung des Maschinenantriebs. Dank des Werkstoffs sind die CFK-Spannmittel um bis zu zwei Drittel leichter als die Standardausführung.
“Wir können fast alle Spannmittel als Carbon-Variante im individuellen Kundenbereich anbieten. Mit der mini-Baureihe haben wir zudem Futter entwickelt, die eine geringere Störkontur und geringere Masse haben. Diese beiden Faktoren spielen bei der Fertigbearbeitung eine immer größere Rolle. Die Zugänglichkeit der Werkzeuge und ein geringerer Energieverbrauch zeichnen ein modernes und zukunftsorientiertes Spannmittel aus. Durch die dynamischeren Spindelbeschleunigungen verkürzt sich die Taktzeit. Und in Summe sinken die Kosten je Werkstück”, beschreibt Nitsche die Lösungsansätze von Hainbuch. Auf der EMO wird das Unternehmen den manuellen Spannstock Manok CFK Leichtbau ausstellen, ebenso die mini-Futterbaureihe und viele weitere Neuheiten, bei denen Nachhaltigkeitsaspekte zum Tragen kommen.
Immer mit Blick auf den Leichtbau fertigt 3D Micro Print durch den Einsatz der Mikro Laser Sinter Technologie hochpräzise Mikrobauteile aus Metall und bietet dem Kunden eine Produktherstellung aus einer Hand sowie einen ganzheitlichen Service. Das Portfolio umfasst den Wissensaustausch, die funktionale Bauteilintegration, das prozessgerechte Design, die Fertigung von Serienteilen sowie auf Nachfrage auch Materialentwicklungen. Dabei sind die Verfahren für höchst auflösende und präzise Mikrobauteile im µm-Bereich ausgelegt. Entwickelt und gefertigt werden sowohl feine Gitterstrukturen als auch Geometrien mit detaillierten Innenstrukturen. Entsprechende Lösungsansätze für verschiedene Branchen wird das Unternehmen auf der EMO in Hannover vorstellen.
Künstliche Intelligenz, Virtual und Augmented Reality sorgen für agileres Arbeiten
Für Maschinenbauer und deren Kunden sind die Themen Nachhaltigkeit und Leichtbau klare Wettbewerbsvorteile in der Wertschöpfungskette und deshalb essenziell. Dies bestätigt auch Autodesk-Technical Sales Manager Steffen Krause: „Mehr als 60 Prozent unserer Kunden haben Erfolgsfaktoren und Ziele, die an die Nachhaltigkeit geknüpft sind – Tendenz steigend. Dies wird durch die Lieferkette auch auf die Dienstleister übertragen.“
Autodesk hat sich auch vor diesem Hintergrund dafür entschieden, unter dem Dach der Automatisierung auf künstliche Intelligenz, Virtual und Augmented Reality sowie 3D-Druck zu setzen. Damit werden Design, Maschinenbau und Simulation bis hin zu CAM, additive Fertigung und Fabrikmanagement digital vereint. „Diese einheitliche Plattform löst die Silos zwischen den Disziplinen auf, ermöglicht agileres Arbeiten zwischen den Ingenieurteams und lässt die Hersteller wettbewerbsfähiger werden”, unterstreicht Krause.
Auf dem Autodesk-Messestand auf der EMO werden sich Besucher anhand der Ausstellungsstücke ein Bild von der CAM-Software verschaffen können. So werden anspruchsvolle komplexe Bauteile mit Freiformflächen zu sehen sein, die zeigen, welch hohe Oberflächenqualität sich mit damit erreichen lässt. Dazu gehören auch Beispiele für die hybride Fertigung, bei der additive und subtraktive Verfahren zusammenspielen. Gezeigt werden zudem Exponate, die die Möglichkeiten für Generatives Design ausloten.
Mit den richtigen Entwicklungstools und einer großen Portion Ingenieurswissen ist in puncto Leichtbau viel möglich. Lediglich die Physik setzt Grenzen. „Aufgrund unseres großen Erfahrungsschatzes konnten wir bisher alle Kundenanforderungen erfüllen. Der Leichtbau, auch in Form von reduzierten Störkonturen, stößt nur an seine Grenzen, wenn die Haltkräfte, die Steifigkeit und die Präzision nicht mehr gewährleistet sind“, unterstreicht Stefan Nitsche von Hainbuch. Thomas Klotz von 3D Micro Print ergänzt: „Leichtbau stößt momentan dann an seine Grenzen, wenn es sich um hochstandardisierte Prozesse und Produkte handelt, die keinen Spielraum für eine Steigerung der Performance zulassen.“
Mit Messdatenerfassung Geometrieabweichungen entgegenwirken
Der 3D-Metalldruck ist auch ein Kompetenzfeld der Rolf Lenk Werkzeug- und Maschinenbau GmbH in Hamburg. Matthias Otte ist verantwortlich für den Bereich additive Fertigung. Er erklärt, worauf es beim Herstellprozess ankommt: „Das Bauteil muss maßhaltig sein. Das heißt: Dem Verzug und der Schrumpfung durch das additive Fertigungsverfahren muss entgegengewirkt werden. Ein wichtiger Punkt dabei ist die optische Geometrieerfassung. Sie erlaubt uns eine schnelle Überprüfung eventuell vorhandener Abweichungen.“
Mithilfe der optischen Messtechnik ist das Unternehmen in der Lage, die komplette Prozesskette der additiven Fertigung zu unterstützen und so passgenauer Bauteile zu fertigen. Dies beginnt bei der Geometrieerfassung des Bauteils, geht weiter über die Erfassung der Abweichungen durch Verzug und Schrumpfung bis hin zur Ergebniskontrolle des fertigen Bauteils. Bereits während der Fertigung können Ungenauigkeiten gegenüber der Sollgeometrie festgestellt werden. Im Bedarfsfall kann darauf dann auch schnell reagiert werden. Zur EMO wird das Unternehmen seine Kompetenzen im Bereich 3D-Druck anhand verschiedener Bauteile vorstellen.
Autorin: Annedore Bose-Munde, Fachjournalistin aus Erfurt
Umfang: rund 9.200 Zeichen inkl. Leerzeichen
EMO Hannover 2019: Die Weltleitmesse auf dem Smartphone
Seite Mitte August ist sie verfügbar: die brandneue App zur EMO Hannover 2019!
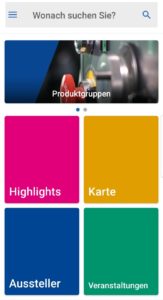
Mit attraktiven Funktionen ist sie der perfekte Messebegleiter und hilft Ihnen von der Planung Ihres Aufenthalts bis zur Erfolgskontrolle. Sie finden die App zum kostenlosen Download im Play Store (Android) und App Store (Apple) unter den Suchbegriffen EMO Hannover und EMO 2019. Einerseits ermöglicht die App einen schnellen Überblick über die Messehighlights. Von IoT in der Produktion und umati über die industrie 4.0 und Start-up Area bis hin zum Additive Manufacturing Circle und Job Board, finden Sie kurze Erläuterungen der jeweiligen Angebote. Übersichten über Sprecher und aktuelle Veranstaltungen der jeweiligen Stände runden den Überblick ab. Andererseits erweist sich die App als treuer Helfer in der Messeplanung. Über das Produkt- und Ausstellerverzeichnis können Sie sich Ihren Messerundgang zusammenstellen und den kürzesten Fußweg inkl. der benötigten Zeit vorschlagen lassen. Der Hallenplan mit Indoor-Navigation zeigt Ihnen nicht nur Ihren exakten Standort an, sondern auch die nächstgelegenen Ein- und Ausgänge sowie Restaurants und Toiletten. Nach Ihrem Login auf der Webseite der EMO Hannover werden Ihre Merkliste sowie Ihre individuell erstellten Laufpläne automatisch in die App synchronisiert. Auch im Rahmen der Erfolgskontrolle bietet Ihnen die App wertvolle Hilfestellung: Setzen Sie Ihren Haken hinter besuchten Ausstellerständen, Vorträgen und Veranstaltungsbereichen und Sie erhalten eine Auswertung, wie viele Ihrer geplanten Programmpunkte Sie bereits sehen konnten. So behalten Sie nicht nur Ihr Wunschprogramm immer im Blick, sondern sehen auch, wie viel Zeit Ihnen für ungeplante Entdeckungen bleibt.
Cobots – Mensch und Roboter gemeinsam zum Erfolg
EMO Hannover 2019 zeigt Robotik- und Automationslösungen für Fertigungsbetriebe
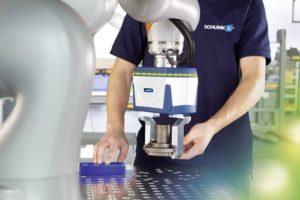
Frankfurt am Main, 12. Juni 2019. – Um als Unternehmen international erfolgreich zu bleiben, gehören Robotik und Automation zu den Schlüsseltechnologien. Cobots interagieren dabei direkt mit dem Menschen und unterstützen Fertigungsbetriebe, sich im Markt produktiv zu behaupten. Auf der EMO Hannover 2019 finden Fachbesucher zahllose Automatisierungslösungen und kollaborative Roboter zur Steigerung ihrer Produktivität.
Mithilfe von Automation und Digitalisierung lassen sich Fertigungsprozesse effizienter gestalten. Von besonderem Interesse sind in diesem Umfeld Cobots – die kollaborativen Industrieroboter arbeiten gemeinsam mit den Menschen ohne spezielle Schutzeinrichtungen wie Zäune oder abgegrenzte Bereiche. In welchen Prozessen kommen Cobots bereits zum Einsatz? Wie lassen sich Kollisionen und damit mögliche Verletzungsgefahren vermeiden? Robotikhersteller, Anbieter verschiedenster Peripheriekomponenten für Automationslösungen sowie Sicherheits- und wissenschaftliche Experten geben einen aktuellen Einblick und Prognosen für künftige Entwicklungen.
Mitarbeiter ergonomisch entlasten
„Für eine intelligente Produktion ist der Mensch unerlässlich“, so Jochen Vetter, Manager Robot Safety bei der Pilz GmbH & Co. KG aus Ostfildern. „Roboter übernehmen z.B. körperlich anstrengende oder monotone Tätigkeiten, während der Mensch höherwertige Aufgaben ausführt. Damit kann die Automatisierung auch Antworten auf Fragen geben, die der demografische Wandel aufwirft.“ Für die Validierung sind bei der Mensch-Roboter-Kollaboration (MRK) unterschiedliche Methoden anzuwenden. Beispielsweise muss zwingend durch ein Messverfahren ermittelt werden, ob mögliche Kollisionen sicherheitstechnisch unbedenklich sind. Hierfür hat Pilz eine eigene Methodik erarbeitet. Ein System misst u.a. die auf den menschlichen Körper einwirkenden Kräfte und vergleicht sie mit den Grenzwerten gemäß der Norm für kollaborative Roboter ISO/TS 15066.
„Die Herausforderung besteht darin, dass sich die Grenzen zwischen den Arbeitsbereichen von Mensch und Maschine auflösen. Zusätzlich zu den vom Roboter ausgehenden Gefahren müssen die Bewegungen des Menschen Berücksichtigung finden“, weiß der Robotik-Sicherheitsexperte. „Diese sind nicht immer kalkulierbar in Hinsicht auf Geschwindigkeit, Reflexe oder plötzlichen Zutritt zusätzlicher Personen. Kollisionen dürfen jedoch zu keinen Verletzungen führen.“ Voraussetzungen dafür seien zuverlässigere Steuerungen und intelligente, dynamische Sensoren am Roboter. Zudem gelte es, durch normative Grundlagen verlässliche Sicherheitsstandards zu setzen.
„Die Interaktion wird sich in Richtung ‚natürlich‘ entwickeln, etwa bei der Sprache und Gestik“, ist Vetter überzeugt. „So wird die MRK für ein anderes Agieren auf eine neue Qualitätsebene gebracht. Darüber hinaus werden MRK-Lösungen in Zukunft an die Fabriksteuerung via OPC UA oder die Industrie 4.0-RAMI-Standards angebunden sein. Sinnvolle Einsatzgebiete sind eher nicht in der Großserienproduktion, sondern bei mittleren und kleinen Serien angesiedelt. MRK macht dann Sinn, wenn die Mitarbeiter ergonomisch entlastet werden, etwa bei Wartungsarbeiten.“
Werkstücke bis 8 kg greifen dank Sicherheitsintelligenz
„Aufgrund der biomechanischen Limits – vorgegeben durch die ISO/TS 15066 – konzentrierte sich der Einsatz von Cobots bislang auf das Handling von Kleinteilen, etwa in Montageanwendungen der Elektronikindustrie oder beim Pick & Place von Gehäusen, Dreh- und Frästeilen etc.“, weiß Prof. Markus Glück, Geschäftsführer Forschung & Entwicklung, Chief Innovation Officer bei der Schunk GmbH & Co. KG, Lauffen/Neckar. „Mit unserem Großhubgreifer EGL-C erschließen wir nun aber eine neue Bauteildimension: Erstmals ist es möglich, formschlüssig gegriffene Werkstücke bis 8 kg sicher zu handhaben. Damit ergeben sich große Potenziale, auch bei Werkzeugmaschinen oder in der Montage.“ Dank integrierter und zum Patent angemeldeter Sicherheitsintelligenz ist es beim Co-act (collaborative actuator) EGL-C gelungen, in kollaborativen Anwendungen Greifkräfte bis 450 N zu realisieren. Das ist rund dreimal so viel wie bisher und stellt eine Weltneuheit dar – auch zu sehen auf der EMO Hannover 2019. „Die MRK wird die Arbeitswelt radikal verändern“, prognostiziert Prof. Glück. „Im Mittelpunkt stehen die Verbesserung der Ergonomie, flexiblere Arbeitsprozesse, Effizienzsteigerung sowie Prozessoptimierung. Mithilfe intelligenter Greifsysteme lassen sich künftig auch höhere Bauteilgewichte handhaben. Zudem werden dank 24V-Technologie Einsätze auf mobilen Plattformen an Bedeutung gewinnen. Ein großes Wachstumspotenzial besitzt darüber hinaus die Montageassistenz durch Leichtbauroboter.“
Eine neue Ära bei der Beladung von Werkzeugmaschinen
„Kollaborative und mobile Robotersysteme bieten neue Möglichkeiten für die Automation von Werkzeugmaschinen. Erstmals kann sich die Automation von ihrem starren Korsett lösen und dank innovativer Robotiklösungen eine Flexibilität und Produktivität in nie gekannter Dimension erreichen“, berichtet Peter Pühringer, Division Manager bei Stäubli Robotics in Bayreuth. Um diese Flexibilität auf die Spitze zu treiben, hat Stäubli die neue TX2-Sechsachser-Generation so universell wie möglich ausgeführt. In der neuen Ausführung eignen sich diese Roboter für die direkte Zusammenarbeit mit dem Menschen. Zudem sind sie als mobile und gleichzeitig kollaborative Robotersysteme erhältlich. „Damit läuten wir eine neue Ära in der Beschickung von Werkzeugmaschinen ein“, ist Pühringer überzeugt. Die Roboter arbeiten sowohl im Stand-alone-Betrieb als auch direkt mit Maschinenbedienern zusammen. Sie können in mobiler Ausführung auf einfachste Art unterschiedliche Werkzeugmaschinen verketten und den kompletten Workflow in Industrie 4.0-Umgebungen übernehmen. „Mit dieser unglaublichen Flexibilität lassen sich völlig neue, digital vernetzte Produktionsprozesse darstellen“, so Pühringer. „Diese werden zu einer signifikanten Steigerung der Produktivität führen und die Wettbewerbsfähigkeit innovativer Unternehmen auf eine neue Stufe stellen. Auf der EMO Hannover stellen wir diese Lösungen einem breiten Publikum vor.“
Sensoren vermeiden mögliche Kollisionen
„Cobots kommen derzeit häufig für einfache Handhabungsprozesse zum Einsatz, u.a. für die Beladung von Maschinen. Dabei werden sie zwar oft schutzzaunlos, aber dennoch mit zusätzlichen Sicherheitseinrichtungen ausgestattet und weniger in einer direkten Mensch-Roboter-Kooperation eingesetzt“, weiß Prof. Gunther Reinhart, Inhaber des Lehrstuhls für Betriebswissenschaften und Montagetechnik am iwb (Institut für Werkzeugmaschinen und Betriebswissenschaften) der TU München. „Aktuelle Arbeiten beschäftigen sich mit der Planungsunterstützung für die MRK, der Sicherheit, aber auch der Instruktion der Roboter. Bezüglich der Sicherheit gehen Innovationen dahingehend, dass mögliche Kollisionen vor Berührung durch unterschiedliche Sensoren – wie kapazitive oder Ultraschallsensoren – oder aber kamerabasiert detektiert werden.“ Der Umgang mit den aktuellen Normen sei derzeit vielen Firmen unklar. „Dabei ist insbesondere zu nennen, wie die Werte in der ISO/TS15066 behandelt werden sollen“, so Reinhart. „Sind die rechtlichen Fragestellungen der Arbeitssicherheit geklärt, werden kollaborative Roboter wohl überwiegend in der Montage zum Einsatz kommen“, wagt Reinhart einen Blick in die Zukunft. „Weitere Anwendungsfälle beziehen sich insbesondere auf eine ergonomische Unterstützung. Dazu muss es jedoch zunächst mehr Roboter für eine MRK mit höherer Traglast geben. Das Institut für Werkzeugmaschinen und Betriebswissenschaften steht den Fachbesuchern der EMO Hannover 2019 für nähere Erläuterungen sehr gerne zur Verfügung.“
Autor: Dag Heidecker, daxTR – Technik + Redaktion, Wermelskirchen (nahe Köln)
((Umfang: rund 7.700 Zeichen inkl. Leerzeichen))
Trockenbearbeitung und MMS erobern immer mehr Anwendungsfelder
Nass oder trocken: EMO Hannover 2019 zeigt vielfältige Technologien (Teil 1)
Frankfurt am Main, 03. September 2019. – Im Fertigungsumfeld stehen Produktionsverantwortliche wiederkehrend vor der Frage: Kommt weiterhin die klassische Zerspanung mithilfe von Kühlschmierstoff (KSS) zum Einsatz oder bieten mir Trockenbearbeitung bzw. Minimalmengenschmierung (MMS) eine Alternative? Mehrere Faktoren beeinflussen diese Entscheidung. In Teil 1 der zweiteiligen Fachartikelserie im Vorfeld der EMO Hannover 2019 nehmen Experten von Schmiersystemen und aus der Wissenschaft Stellung. Werkzeug- und Maschinenhersteller beleuchten die Thematik als Anwender in der Praxis im zweiten Teil.
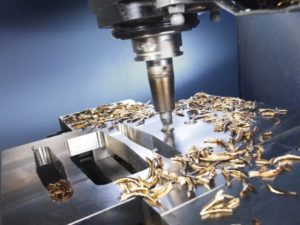
Foto: bielomatik Leuze
Während der Zerspanung entstehen in der Schnittzone besonders hohe Temperaturen. Kühlschmierstoffe verringern hierbei die Reibung, sorgen für Kühlung – allerdings unter Umständen auch für zerstörende Thermo-schocks – und unterstützen den Abtransport der Späne. Nachdem Experten um die Jahrtausendwende einige Experten einen Durchbruch der Trockenbearbeitung als substituierendes Verfahren prognostizierten, ist es Zeit, nach dem aktuellen Stand der Technik zu fragen. In welchen Bereichen konnte sich dieses Verfahren oder auch die Minimalmengenschmierung als Quasi-Trockenbearbeitung mit welchem Umfang durchsetzen? Für eine umfassende Einschätzung aus verschiedenen Blickwinkeln nennen Schmiersystemhersteller, Maschinen- sowie Werkzeuganbieter und Wissenschaftler in dem zweiteiligen Fachbericht die Vor- und Nachteile der genannten Technologien.
Serienbearbeitungen besonders interessant
„Der Hauptanwendungsbereich für die Minimalmengenschmierung liegt in der Bearbeitung von Urformteilen, wie sie in der Großserienfertigung in der Automobilindustrie – insbesondere im Powertrain – vorkommen. Das geht vom Zylinderkopf und Motorblock über Kurbel- oder Nockenwelle, Pleuel, Getriebegehäuse, Radträger etc.“, weiß Jürgen Keppler vom Technischen Vertrieb der bielomatik Leuze GmbH + Co. KG in Neuffen. Das Maschinenbauunternehmen aus Baden-Württemberg gilt als anerkannter Spezialist für die Entwicklung und Herstellung hochwertiger MMS-Systeme. „Weitere Einsatzbereiche im Industrieumfeld sind die Bearbeitung kubischer Bauteile und die Gussbearbeitung im Maschinenbau, wie Armaturen, Pumpengehäuse oder Ventile. Auch in der Luftfahrtindustrie ist es ein großer Vorteil, wenn komplexe Bauteile nicht mit Emulsion überschwemmt werden.“
Der Experte schätzt, dass bei Neuinvestitionen im Großserienbereich circa 15 Prozent der Bauteile mit MMS bearbeitet werden, wobei z.B. beim Tieflochbohren in Kurbelwellen bis zu 70 Prozent erreicht werden. „In den oben genannten Anwendungsgebieten wird sich die MMS-Bearbeitung aber weiter durchsetzen“, ist Keppler überzeugt. „Der vor rund 20 Jahren prognostizierte Aufschwung der MMS-Bearbeitung ist hauptsächlich im Automotive-Bereich eingetreten. Hier konnten bei den Guss- und Schmiedeteilen prozesstechnisch die Vorteile der MMS voll ausgeschöpft und andererseits – angesichts der hohen Stückzahlen – die damit verbundenen F&E-Maßnahmen gestemmt werden. Auch mit den bevorstehenden Veränderungen im Zusammenhang mit der E-Mobilität und der additiven Fertigung wird es neue Anwendungsbereiche geben. Der große Vorteil der MMS liegt in der Kosteneinsparung bei den Ressourcen Öl, Wasser und Energie.“ Weitere Vorteile seien trockene Werkstücke, keine Verschleppung von Emulsion mit der einhergehenden Verschmutzung in den Fertigungshallen und die Verhinderung der damit verbundenen gesundheitlichen Risiken. „Durch die ständigen Weiterentwicklungen bei Werkstoffen und Anwendungen werden auch immer neue Anforderungen an die Zerspanungsprozesse und somit an die MMS-Systeme gestellt, was sicherlich noch interessante Lösungen hervorbringen wird“, so Keppler.
Was sagt die Wissenschaft?
„Durch moderne Schneidstoffe ist die Trockenbearbeitung in nahezu allen Bereichen der spanenden Fertigung angekommen. Der zunehmende Kostendruck, aber auch energieverbrauchs- und ökologische Aspekte sorgen für eine Renaissance dieser Technologien“, sagt Abteilungsleiter Zerspanung Dr. Ivan Iovkov vom Institut für Spanende Fertigung ISF der Technischen Universität Dortmund. „Nicht nur beim klassischen Fräsen
oder Drehen hält die Trockenbearbeitung Einzug, auch bei anspruchsvollen Verfahren wie z.B. dem Tiefbohren und dem Wälzfräsen bestehen Bestrebungen, den KSS-Einsatz zu minimieren oder komplett zu vermeiden. Nach wie vor ist aber eine gewisse Anpassung der Zerspanprozesse und der Technologie erforderlich.“ Tendenziell sei bei großen Unternehmen mit hohen Stückzahlen die Trockenbearbeitung stärker verbreitet als bei kleineren Firmen mit variierenden, hochgenauen und komplexen Komponenten.
„Aus meiner Sicht wird es in Zukunft sowohl Trocken- als auch Nassbearbeitung geben“, so seine Prognose. „Wir benötigen für die richtige Entscheidung einen ganzheitlichen Blick auf die Fertigung, ob eine Trockenbearbeitung sinnvoll ist und wann diese unverhältnismäßig hohe Prozessanpassungsaufwände verlangt. Aufgrund der stetigen Weiterentwicklung der MMS-Gerätetechnologie und der Beschichtungen sowie der zunehmenden Genauigkeit des Maschinenparks, aber auch der Digitalisierung, beispielsweise durch In-Prozess-Sensorüberwachung relevanter Größen, wird es in Zukunft möglich sein, zunehmend mehr Zerspanprozesse trocken oder mit MMS unter robusten Bedingungen durchzuführen.“
Resümee
Von einer umfassenden Ablösung klassischer Zerspanungsprozesse durch die Trockenbearbeitung oder Minimalmengenschmierung kann zwar nicht gesprochen werden, denn insgesamt machen die Nassbearbeitungen mit umfangreicheren Mengen an Kühlschmierstoff geschätzt immer noch über 85 Prozent des Anteils aus. Nichtsdestotrotz erobern sich die trockenen Verfahren immer mehr Bereiche sowohl im allgemeinen Zerspanungsumfeld als auch insbesondere in speziellen Gebieten. Im später folgenden zweiten Teil des Fachartikels werden darüber hinaus Werkzeuge- und Maschinenhersteller praxisnah Stellung zu den verschiedenen Fertigungstechnogien nehmen sowie Empfehlungen für eine ganzheitliche Betrachtung geben. Um für die eigenen Anwendungen die passende Technologie zu finden, erhalten Fachbesucher auf der EMO Hannover 2019 für jeden Fall umfassende Informationen und Unterstützung.
Autor: Dag Heidecker, daxTR – Technik + Redaktion, Wermelskirchen
(Umfang: rund 6.300 Zeichen inkl. Leerzeichen)
Digital und nachhaltig zugleich – geht das?
EMO Hannover 2019: Digitale Wege zur nachhaltigen Zerspanung
Frankfurt am Main, 03. September 2019. Industrielle Prozesse sind entweder digital oder nachhaltig – das zumindest denkt so mancher, der sich mit dem Thema noch nicht auseinandergesetzt hat. Doch das VDMA-Technologieforum auf der EMO Hannover beweist das Gegenteil: Sinnvoll und clever angewandt, kann Digitalisierung die Nachhaltigkeit sogar steigern. Es kommen vier Firmen zu Wort, die mit ihren digitalen Lösungen dazu beitragen, dass Werkzeuge nachhaltiger hergestellt werden oder dass sich mit ihnen nachhaltiger zerspanen lässt.
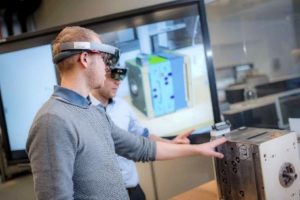
Foto: Phoenix Contact
Smart Service ist für Konrad Keck, Vertriebsleiter DACH der Benz GmbH Werkzeugsysteme aus Haslach im Kinzigtal (bei Offenburg) das Zauberwort, um Dienstleistungen und Produkte reif für Industrie 4.0 (IoT-ready) zu machen. Darunter verstehen die Badener ein Gesamtservice-Konzept, bei dem immer mehr digitale Informationen etwa von Sensoren zur vorbeugenden Service-Abwicklung beitragen.
Energy Harvesting versorgt Sensoren mit Strom
Manchmal steckt der technische Teufel dabei im Detail: So verbrauchen Sensoren oft zusätzliche Energie. Keck nennt die Alternative: „Bei rotierenden Werkzeugen wird die Energie für das Sensorsystem mittels Energy Harvesting erzeugt und somit weitestgehend auf Batterielösungen verzichtet.“ Anwender von Energy Harvesting „ernten“ elektrische Energie aus Quellen wie Umgebungstemperatur, Vibrationen oder Luftströmungen, um so mobile Geräte oder Elektronik mit geringer Leistung zu versorgen.
Der nachhaltigste Effekt liege beim so genannten Smart Service jedoch darin, dass die Werkzeuge durch vorbeugende Wartungsintervalle länger halten. Wenn künftig Produkte dank Digitalisierung ihren Zustand kennen, lassen sich mit diesen Kennwerten Regelkreise aufsetzen, die die Standzeit der Werkzeuge erhöhen. Wie sich die Digitalisierung in der Praxis auf Anwendungen auswirkt, demonstrieren die Badener in Hannover unter anderem an dem neu entwickelten Spindelreihenmagazin Benz Hybrix und der Stoßaggregate-Familie LinA, die nun IoT-ready sei.
Auf der EMO Hannover 2019 präsentiert Daniel Meuris, Leiter Digitalisierung und Virtualisierung beim Werkzeugmaschinenhersteller Klingelnberg GmbH, Hückeswagen, die Plattform GearEngine für die Verzahnungsproduktion. Sie dient als zentrale Sammelstelle von Produktionsdaten und Schnittstelle zwischen Produktions- und Unternehmensebene. Die Plattform erlaubt es dem Betreiber von Klingelnberg-Werkzeugmaschinen, softwarebasierte Datendienste auf einfache Art und Weise einzusetzen.
Software-Tool erhöht die Werkzeugeffizienz
Als Schlüssel zur nachhaltigen Zerspanung bezeichnet Meuris die Werkzeugeffizienz. Ein Beispiel ist die Kegelradfertigung, bei der sich die Effizienz bisher wegen der dort eingesetzten Spezialwerkzeuge und mangelnder Daten nicht analysieren ließ. Das neue SmartTooling-System von Klingelnberg kann dagegen Werkzeuge und Vorrichtungen für Kegelrad-Fräsmaschinen mit Hilfe von Data Matrix Codes identifizieren und in einer Datenbank zentral verwalten. Meuris: „Die Produktionsmittel werden durch einen digitalen Zwilling beliebig genau beschrieben und liegen in einer zentralen Datenbank vor, die während und nach der Verzahnung mit Produktionsdaten erweitert wird.“ Wie das in der Praxis funktioniert, führt Klingelnberg in Hannover beim Einsatz an der Maschine vor.
Wie sich mit Werkzeugdaten die Fertigung optimieren lässt, beschreibt Dr. Raphael Rohde, Mitarbeiter im Technology Development der Business Unit Tools and Parts der Phoenix Contact GmbH & Co. KG, auf dem Technologieforum der EMO Hannover. Der Hersteller von Verbindungs- und Automatisierungstechnik vernetzt seine Spritzgießwerkzeuge mit Hilfe der Datenerfassung über RFID-Technologie sowie optische Marker. „Die Herstellungs- sowie Produktionsinformationen sind stets und umfassend verfügbar“, erklärt Rohde. „Dem Mitarbeiter und dem Kunden werden die Daten benutzerspezifisch in Form von Visualisierungsboards oder durch die Verwendung von Augmented Reality zielorientiert aufbereitet zur Verfügung gestellt. Fehlleistungen durch falsche Interpretation bzw. Folgefehler können auf diese Weise auf ein Minimum reduziert werden und tragen so zur Nachhaltigkeit in der Produktion bei.“
Messtechnik unterstützt die digitale Transformation
Die Messtechnik zieht wegen der Digitalisierung der Industrie näher an oder in die Produktion, beobachtet Prof. Heiko Wenzel-Schinzer, Geschäftsführer und Chief Digital Officer der Wenzel Group GmbH & Co. KG in Wiesthal: „Wir messen mehr, durch optische Lösungen, 5-Achsmesskopf oder spezielle Messmaschinen schneller und geben dank geschlossener Regelkreise direktes Feedback an die Bearbeitungsmaschinen.“ Wenn die Messtechnik aber in die Fertigung wandere, sei es unabdingbar, dass die Ausfallzeiten gegen Null gehen. Daher biete der Messtechnik-Produzent zusätzliche Lösungen an, um Probleme an den Maschinen bereits sehr frühzeitig zu entdecken und zu korrigieren. Das erhöht die Lebensdauer der Produktionstechnik und macht sie nachhaltiger.
Aber auch die Messmaschinen von Wenzel seien für extrem lange Nutzlaufzeiten ausgelegt. „Auf diesem Fundament setzen wir moderne Messtechnik ein, die immer wieder modernisiert werden kann, ohne dass die komplette Maschine ausgetauscht werden muss“, erklärt der Geschäftsführer. „Der geschlossene Regelkreis zwischen Messtechnik und Bearbeitungsmaschinen reduziert Ausschuss, da wir – Stichwort Prozessüberwachung – sehr frühzeitig Rückmeldungen über Fertigungsprobleme geben können.“ Wie unter diesen Aspekten das Zusammenspiel der Fertigung mit neuer Messtechnik – vom portablen Messarm bis hin zur Highspeed-Scanning-Maschine – funktioniert, zeigt die Wenzel Group Besuchern der EMO Hannover an ihrem Stand.
Mehr über Nachhaltigkeit und Digitalisierung in der Produktion erfahren Interessenten auf dem Technologieforum der VDMA-Fachverbände Präzisionswerkzeuge sowie Mess- und Prüftechnik in Halle 4, Stand D39.
Autor: Nikolaus Fecht, Journalist aus Gelsenkirchen
Umfang: rund 5800 Zeichen inkl. Leerzeichen
Smarte Software auf der EMO Hannover
Frankfurt am Main, 03. September 2019. – Ingenieuren lästige Routinen abnehmen, um mehr Freiraum für kreative Tätigkeit zu schaffen: die AMendate GmbH aus Paderborn will die additive Fertigung auf ein neues Niveau heben. Mit einer Software, die pünktlich zur EMO Hannover Marktreife erlangen soll, wird das junge Unternehmen am Start-Up-Gemeinschaftsstand auf der Fachmesse die Neuentwicklung präsentieren. Das Ziel der westfälischen Gründer: Bekanntheit erlangen und schon bald den Markt für generatives Design dominieren.
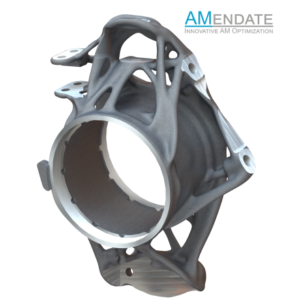
Foto: AMendate GmbH
Am Anfang standen vier Freunde, die am Forschungszentrum für additive Fertigung (DMRC) der Universität Paderborn in über vier Jahren Forschung eine wichtige Beobachtung machten: obwohl der industrielle 3D-Druck vielfältige Möglichkeiten bietet, filigrane Leichtmetallbauteile mit großer Robustheit kostengünstig herzustellen, fehlte es an der passenden Software. Die manuelle Datenübertragung in CAD-Formate kostete viel Zeit und Aufwand, ließ überdies große Interpretationsspielräume, die zu Qualitätsverlusten führten. „Dieses Problem wollten wir lösen“, sagt Dr. Thomas Reiher, der sich im Rahmen seiner Dissertation mit der Erzeugung komplexer bionischer Strukturen beschäftigt hat und als Geschäftsführer zum Gründungsteam der AMendate GmbH gehört. Über vier Jahre hat er an der Entwicklung einer Technologie mitgearbeitet, die den Prozess der Datenübertragung automatisiert, interpretiert und die entstehenden Geometriedaten intelligent glättet. Hieraus entwickelte sich der Ansatz zur Unternehmensgründung, um die Technologie anwenderorientiert weiter zu entwickeln.
Mehr Zeit für Wertschöpfung statt kleinteiliger Datenübertragung
Entstanden ist eine Software, die die Qualität additiv gefertigter Bauteile erhöht, Prozesse erheblich beschleunigt und nach letztem Feinschliff im Sommer am Markt gelaunched wird. Reiher: „Unsere Software sorgt dafür, dass Geometrien bei der Datenglättung nicht mehr unbeabsichtigt entfernt werden. Außerdem sind Arbeitsschritte, die sonst einige Wochen in Anspruch nehmen, mit der Technologie in wenigen Tagen zu erledigen“.
Befürchtungen, Fachkräfte könnten über die Automatisierung überflüssig werden, treten die Jungunternehmer dabei entschieden entgegen. Dr. Gereon Deppe, zuständig für Marketing und Finanzen sowie Mitgründer des Start-Ups, sieht ihren Stellenwert in der Wertschöpfung sogar steigen: „Statt sich im Klein-Klein der Datenbearbeitung zu verlieren, können Ingenieure dem kreativen Prozess wesentlich mehr Aufmerksamkeit widmen. Sie gewinnen Zeit, um das grundlegende Konzept des Produkts zu optimieren und zusätzliche Features zu integrieren.
Dass dieser Ansatz das Potenzial besitzt die additive Fertigung zu revolutionieren, wird in der Fachwelt bereits gesehen. Die Leser des Branchenportals 3Dnatives kürten AMendate in einer internationalen Abstimmung zum innovativsten Start-Up des Jahres 2018. Ein Exist-Gründerstipendium für drei Mitarbeiter konnte das Unternehmen ebenfalls an Land ziehen. Gemeinsam mit der Protiq GmbH aus Blomberg, einem bereits etablierten Anbieter der additiven Fertigung, gelang zudem eine weitreichende Kooperation. Auf Basis von AMendates Technologie bietet Protiq nun als erster Dienstleister weltweit eine Online-Topologieoptimierung, die über einfache Bedienbarkeit einen Mehrwert für Anwender schafft.
Vielfältige Anwendungsgebiete für Leichtbauteile
Geht es nach den Gründern, wird die additive Fertigung mit ihrer Lösung den Schritt von einer vielversprechenden Technologie zu einer Schlüsseltechnologie gehen. Reiher: „Bedarf an filigranem Leichtbaudesign herrscht von der Luftfahrt- und Autoindustrie bis hin zum Maschinen- und Anlagenbau in vielen Bereichen, gerade auch wenn wir an Sondermaschinen mit kleinen Stückzahlen denken. Wir bieten ein bisher nicht verfügbares Werkzeug, das schnell benutzbare Bauteile generiert, den Materialeinsatz reduziert und einen kostengünstigen Einsatz ermöglicht.“ Im Fokus stehen nicht nur etablierte Kunden und Produkte, deren bislang klassisch hergestellte Bauteile einem Redesign zur additiven Fertigung unterzogen werden sollen, sondern auch neue Bauteile, die originär aus dem 3D-Drucker stammen.
Als Marktführer für Wachstum sorgen
Derzeit arbeitet das Team an einer intuitiven Benutzeroberfläche, die eine Bauteiloptimierung ohne umfangreiches Vorwissen ermöglicht und damit auch kleinere Unternehmen in die Lage versetzt, additive Fertigung in ihrer Produktion einzusetzen. Deppe: „Wir haben das Ziel, den Markt des generativen Designs wesentlich mitzugestalten, und die Vision, dass zukünftig alle Bauteile optimiert werden. So können Rohstoffe geschont und eine Produktion im Sinne der Nachhaltigkeit vorangetrieben werden“. Um diese Vision Realität werden zu lassen, strebt AMendate schnelles nationales und internationales Wachstum basierend auf seiner Technologieführerschaft an. Der derzeit noch kleine Markt biete dafür eine gute Voraussetzung, ist Deppe überzeugt: „Es ist noch immer sehr schwer, Erfahrungswerte, ausgeprägte Kompetenz oder passende Angebote zu finden. Hier können wir ansetzen, den Markt selbst entwickeln und Prozesse aktiv vorantreiben.“
EMO Hannover als Plattform zur Kundenakquise
Die EMO Hannover soll dabei helfen. Die Existenzgründer setzen ganz auf den internationalen Stellenwert der Weltleitmesse der Metallverarbeitung, erhoffen sich Kontakt zu Neukunden und Interessierten aus den wichtigsten Industrien und Absatzmärkten. „Es ist ein gutes Gefühl, mit Fachleuten ins Gespräch zu kommen und zu sehen, dass die eigene Idee ankommt. Messeauftritte helfen uns dazuzulernen und die Bedürfnisse noch besser einzuschätzen“, so Reiher, der mit seinem Team auf der EMO Hannover kurz vor dem ersten Unternehmensgeburtstag stehen wird. Auch das Messemotto Smart technologies driving tomorrow’s production! sei den Gründern auf den Leib geschnitten, freut sich Deppe: „Wir digitalisieren einen manuellen Prozess, der gestützt durch künstliche Intelligenz zukünftig autonom stattfinden kann. Das macht uns zum Enabler der additiven Fertigung im Massenmarkt, einer echten Triebfeder der Produktion von morgen.“
Autor: Stefan Schwaneck, VDW
Umfang: 6.206 Zeichen inkl. Leerzeichen
Hersteller setzen vermehrt auf Trockenbearbeitung und MMS
EMO Hannover 2019 gibt Entscheidungshilfen für eigene Anwendungen (Teil 2)
Frankfurt am Main, 03. September 2019. –Kommt im Fertigungsumfeld weiterhin eher die klassische Zerspanung mithilfe von Kühlschmierstoff (KSS) zum Einsatz oder bieten Trockenbearbeitung bzw. Minimalmengenschmierung (MMS) eine Alternative? Aus technologischer Sicht gilt es, Werkstoffeigenschaften und Maschinenleistung zu berücksichtigen, aber auch Anlagenkosten, Energie und Gesundheitsaspekte sind zunehmend in die ganzheitliche Prozessbetrachtung einzubeziehen. Im ersten Teil der Fachartikelserie nahmen Schmiersystemhersteller und die Wissenschaft Stellung zu dem Thema. Teil 2 beleuchtet nun aus der praxisnahen Sicht von Werkzeug- und Maschinenherstellern verschiedene Zerspanungstechnologien: eine Vorschau auf die EMO Hannover 2019.
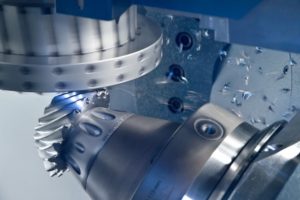
Vor gut zwei Jahrzehnten sahen einige Experten bereits einen Siegeszug der Trockenbearbeitung voraus. In welchen Bereichen konnte sich dieses Verfahren oder auch die Minimalmengenschmierung durchsetzen?
Zahnradfräsen ausschließlich trocken
„Die Vorteile der MMS gegenüber der Nassbearbeitung sind geringere Kosten des Kühlschmierstoffes und der Entfall chemischer Zusätze im KSS. Das führt zu Kostenvorteilen und einer geringeren Gesundheitsbelastung der Mitarbeiter“, weiß der Leiter Technologie & Innovation Dr. Hartmuth Müller vom Produktionsstandort Hückeswagen bei der Klingelnberg GmbH. Das weltweit rund 1.300 Mitarbeiter beschäftigende Maschinenbauunternehmen mit Hauptsitz in Zürich (Schweiz) ist unter anderem auf das Gebiet der Kegel- und Stirnrad-Technologie spezialisiert.
„Das Wirkprinzip der MMS beruht auf der Benetzung der Spanfläche. Mit innengekühlten Werkzeugen ist dies einfach zu erreichen, während es sich bei den komplizierten Werkzeuggeometrien der Verzahnwerkzeuge nicht sinnvoll realisieren lässt. Aus diesem Grund setzt Klingelnberg beim Zahnradfräsen ausschließlich auf die Trockenbearbeitung. Die MMS kommt hausintern nur für die Bearbeitung von Gusskomponenten im Maschinenbau zum Einsatz.“ Zum Kegelradfräsen werden Hartmetall-Stabmesserwerkzeuge eingesetzt. Beim Stirnradfräsen sind Hartmetall-Werkzeuge aus Kostengründen wenig verbreitet, in aller Regel wird hier mit PM-HSS-Wälzfräsern in Trockenschnitt gearbeitet. Die anschließende Hartfeinbearbeitung von Zahnrädern erfolgt – wann immer es geht – durch Schleifen mit Öl als Kühlschmierstoff.
„Der prognostizierte Siegeszug der Trockenbearbeitung ist in der Zahnradfertigung in vollem Umfang eingetreten“, so Dr. Müller. „Durch die Entwicklungen bei Schneidstoffen und Beschichtungen sind die Schnittgeschwindigkeiten bis zu fünfmal so hoch wie in der Nassbearbeitung vor 20 Jahren. So hat die Trockenbearbeitung neben einer erheblichen Produktivitätssteigerung auch zu einer saubereren Fertigung geführt.“ Auf der EMO Hannover zeigt Klingelnberg seine hohe Kompetenz in der Verzahnungsindustrie, u.a. die Entwicklung und Herstellung von Maschinen für die Fertigung von Verzahnungen, von Präzisionsmesszentren für rotationssymmetrische Objekte aller Art sowie die Fertigung hochpräziser Getriebekomponenten im Kundenauftrag.
Kosteneffizient und umweltschonend
Zu den führenden Werkzeugherstellern gehört die Hartmetall-Werkzeugfabrik Paul Horn GmbH aus Tübingen. „Die MMS hat den konventionellen Kühlschmierstoff in einigen Zerspanprozessen verdrängt“, weiß Geschäftsführer Lothar Horn. „Kühlen und schmieren mit der Minimalmengenschmierung bietet dem Anwender eine Reihe von Vorteilen. Diese haben dazu geführt, dass die MMS vor allem im Bereich der Serienfertigung für viele Zerspanoperationen zum Einsatz kommt. Diese Art der Kühlung spart hohe Kosten in der Pflege, Aufbereitung und Entsorgung herkömmlicher Kühlschmierstoffe. Des Weiteren entfallen die Energiekosten für Hochdruck- und Förderungspumpen zurück zum Sammelbecken. Zusätzlich erhöht der Gesetzgeber die Anforderungen an die KSS in Bezug auf gesundheitsgefährdende Inhaltstoffe. Trotz der genannten MMS-Vorteile ist der konventionelle KSS aus den Fertigungsstätten aber nicht wegzudenken. Viele Prozesse – zum Beispiel die Bohrungsbearbeitung, das Zerspanen von hochwarmfesten Legierungen sowie die Innenbearbeitung mit einem hohen Spanabtrag – verlangen die ausreichende Versorgung mit einem konventionellen Kühlschmierstoff.“ Auf der EMO Hannover 2019 sind die Werkzeugspezialisten mit ihrem umfangreichen Portfolio zum Drehen, Fräsen, Nutstoßen und Reiben sowie mit hochharten Schneidstoffen, Sonderwerkzeugen etc. vertreten.
Trockenbearbeitung richtig planen
„Bei Maschinen der Firma Grob wird eine Trocken- bzw. MMS-Bearbeitung bei Prozessen mit einer geometrisch bestimmten Schneide wie Bohren, Fräsen oder Schruppen eingesetzt“, berichtet Jochen Nahl, CSO der Grob-Werke GmbH & Co. KG aus Mindelheim. „Typische Werkstücke sind Rahmenstruktur- oder Fahrwerksteile, Bauteile des Verbrennungsmotors und des Antriebsstrangs aus Aluminium oder Grauguss und inzwischen sogar Turboladergehäuse aus hochwarmfestem Stahlguss. Obwohl die Nassbearbeitung in vielen Unternehmen noch fester Teil der Firmenphilosophie ist, kletterte der Anteil von MMS-Maschinen in den letzten Jahren bereits auf 12 Prozent und steigt besonders bei der Bearbeitung von Rahmenstruktur- und Fahrwerksteilen weiterhin kontinuierlich an.“ Seit über 90 Jahren ist das Familienunternehmen mit heute circa 6.900 Mitarbeitern weltweit taktgebender Vorreiter im Bau hochinnovativer Produktions- und Automatisierungssysteme. „Die Vorteile einer MMS-Bearbeitung sprechen für sich“, führt Jochen Nahl weiter aus. „Die Investitionskosten für die Fertigungslinie können gesenkt und der Aufwand zur Werkstückreinigung kann entscheidend reduziert werden. Außerdem lässt sich im Vergleich zur Nassbearbeitung rund ein Viertel Energie einsparen.“
Obwohl der Einsatz der Trockenbearbeitung bis heute nicht in der erwarteten Dimension eintraf, sei zu erkennen, dass sich die Branche sukzessive darauf einstelle. „Um von den Vorteilen zu profitieren, sollte ein erfolgreicher Umstieg von der Nass- zur Trockenbearbeitung immer entlang einer durchdachten Strategie und mit einem kompetenten Maschinenlieferanten als Partner realisiert werden“, empfiehlt CSO Nahl. „So können moderne Unternehmen bereits heute von den neuesten Entwicklungen wie einer einträglichen Temperaturkompensation, dem Einsatz höheren Luftdrucks und modular aufgebauten Systemen profitieren, die in der Folge Fertigungskosten reduzieren und unnötiges Over-Engineering vermeiden.“ Der Global Player mit Stammsitz in Mindelheim (Bayern) präsentiert auf der diesjährigen EMO in Hannover sein aktuelles Produktportfolio sowie Live-Bearbeitungen und technische Highlights.
Fazit und Ausblick
Noch immer machen die Nassbearbeitungen mit umfangreicheren Mengen an Kühlschmierstoff den bei weitem größten Anteil der Zerspanungsprozesse aus. Trotzdem sind Trockenbearbeitung bzw. Minimalmengenschmierung auf dem Vormarsch, gerade auch in speziellen Gebieten wie beispielsweise dem Zahnradfräsen.
Bei der Auswahl des geeigneten Verfahrens spielen neben technologischen Aspekten, wie zu bearbeitender Werkstoff und Maschinenperformance, mögliche Kosteneinsparungen bei Energie und Anlagen eine wesentliche Rolle. Darüber hinaus fließen aber auch gesundheitliche Aspekte, Nachhaltigkeit sowie verschärfende Auflagen zunehmend in die ganzheitlichen Betrachtungen ein. Technologische Fortschritte und detaillierte Kenntnisse über die Vorgänge direkt an der Schneide bieten künftig zunehmend mehr Möglichkeiten, mithilfe der Trockenbearbeitung oder MMS sicher und oft auch hochproduktiv zu zerspanen. Auf der EMO Hannover 2019 finden Fachbesucher ausführliche Informationen, Anregungen und Hilfe, um für die eigenen Anwendungen die richtige Wahl zwischen Nass- und Trockenbearbeitung bzw. MMS zu treffen.
Autor: Dag Heidecker, daxTR – Technik + Redaktion, Wermelskirchen</em
(Umfang: rund 7.900 Zeichen inkl. Leerzeichen)
Gestalt Robotics automatisiert die Industrie
Start-up-Area auf der EMO Hannover 2019 präsentiert viele spannende Newcomer
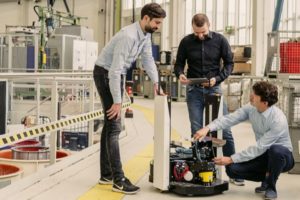
Bild: Gestalt Robotics
Frankfurt am Main, 03. September 2019.– Start-ups sind gefragt. Viele etablierte Unternehmen suchen den Kontakt, wollen kooperieren und/oder investieren. Ein derart gesuchter Gesprächspartner ist auch Thomas Staufenbiel, einer von drei Gründern der Gestalt Robotics GmbH in Berlin. Sie stellt zur EMO Hannover auf dem Start-up-Stand des Bundeswirtschaftsministeriums in Halle 9 ihre maßgeschneiderte Software für Automatisierung und Künstliche Intelligenz (KI)vor.
Diese Software wird beispielsweise in der industriellen Bildverarbeitung und Werkerassistenz sowie in autonomen Transport- und intelligenten Robotersystem eingesetzt. Das klingt abstrakt. Wir begleiten Thomas Staufenbiel an seinem Arbeitsplatz. Ein typisches Forschungsprojekt, an dem er und zehn weitere Mitarbeiter gerade tüfteln, ist ein Werker-Assistenzsystem. Es soll Montagetätigkeiten erleichtern, indem es mit Hilfe von Augmented Reality den Monteur über die nächsten Schritte informiert und den besten Weg dorthin. „Damit soll der Werker unterstützt und die Qualität beim Produkt verbessert werden“, sagt Staufenbiel. Noch ist nicht klar, wie das Assistenzsystem umgesetzt wird, ob mit einer 3D-Brille oder über ein Displaysystem. Aber dafür wird das System im Rahmen eines Forschungsprojekts entwickelt, in dessen Rahmen diese Entscheidungen vorab genau untersucht werden.
Engagement in Forschungsprojekten fördert Zugang zu etablierten Partnern
„Es ist nicht so einfach, den Zuschlag für die Teilnahme an einem Forschungsprojekt zu erlangen“, räumt Staufenbiel ein. „Aber es lohnt sich, wenn wir gemeinsam mit etablierten Akteuren in einem Konsortium sitzen und unsere Kompetenz beweisen können.“ Gerade bei den Assistenzsystemen spielt auch die Akzeptanz der Menschen, die sie unterstützen sollen, eine wichtige Rolle. Untersuchungen dazu gehören in jedes Projekt dieses Bereichs.
Ein weiteres probates Mittel, Öffentlichkeit herzustellen und sich ins Gespräch zu bringen, ist die Teilnahme an Messen. Das produzierende Gewerbe ist ein wichtiger Zielmarkt für Gestalt Robotics. Um ihren Bekanntheitsgrad in diesem Umfeld zu erhöhen, beteiligt sich das Unternehmen an der EMO Hannover 2019. „Wir wollen insbesondere industrielle Kontakte zu Entwicklungs- und Forschungsleitern größerer produzierender Unternehmen herstellen und die Strategie potenzieller Nutzer unserer Software verstehen lernen“, begründet Staufenbiel die Anmeldung zur EMO Hannover. Erfahrungen mit Messeteilnahmen bestehen bereits.
Gestalt Robotics wurde 2016 gegründet von einem Raketeningenieur, einem Roboterfachmann und einem Vision-Experten. Die Ursprungsidee bestand in der Softwareentwicklung für mechatronische Systeme. Dann kam die Robotik hinzu, gespickt mit Kameras und Bilderkennung. „Gestalt bezeichnet ja die äußere Form, den Umriss oder die Erscheinung. Da wir uns viel mit Wahrnehmung beschäftigen, erschien uns dieser Name passend“, erläutert Staufenbiel.
Das Unternehmen plant im laufenden Jahr eine Verdoppelung des Umsatzes. „Angesichts des gewaltigen Bedarfs in der Industrie rechnen wir damit und hoffen natürlich auch, dass sich diese Entwicklung fortschreiben lässt“, ist Staufenbiel zuversichtlich. Die Kunden kommen hauptsächlich aus dem Automotive-Bereich, sind Robotik-Anwender oder sind Komponentenzulieferer, die ihre Produktion verbessern wollen. Bei der Personalentwicklung jedenfalls sieht er derzeit keine großen Probleme. „Wir sind attraktiv für junge Leute, weil wir breit aufgestellt sind und Mitarbeiter ihre Kompetenzen in unterschiedlichen Projekten weiter auf- und ausbauen können“, sagt Gründer Staufenbiel.
Autor: Sylke Becker, Zeichen: 3709 mit Leerzeichen